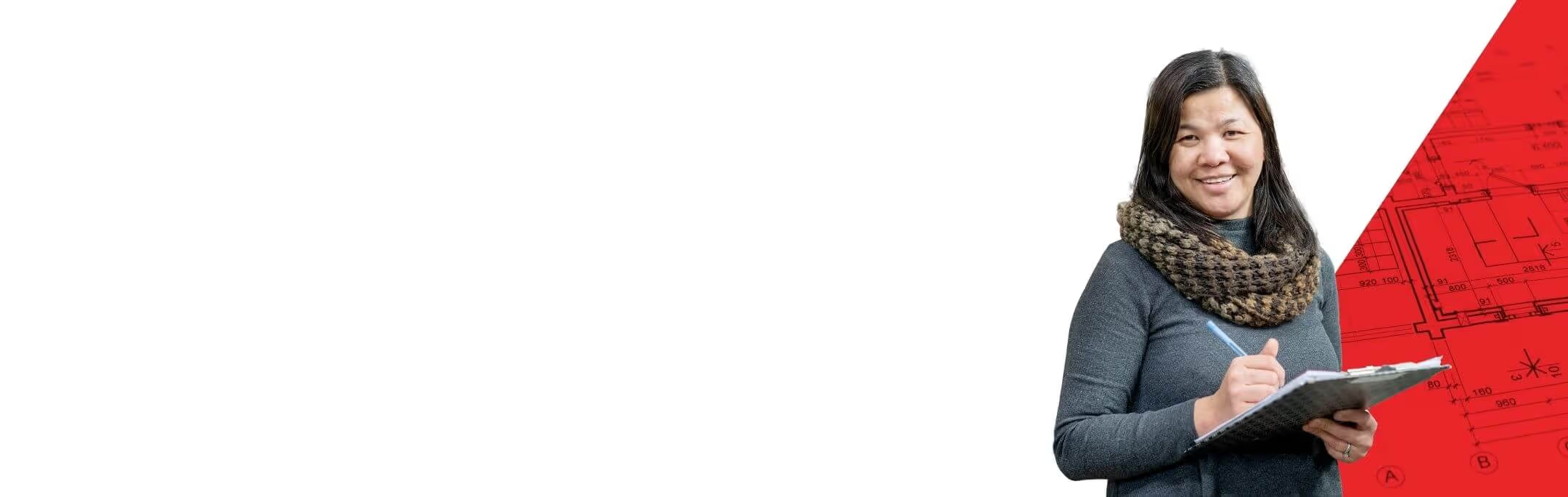
Powering Knowledge: Bailey Blog
At Bailey, we know that knowledge fuels innovation. Our blog is your go-to resource for expert insights, industry trends, and practical guides—helping you stay ahead in hydraulics and electronic solutions.
All Our Educational Articles
For over 40 years, Bailey has been a trusted leader in the manufacturing and distribution of hydraulic and electronic solutions. Dive into our educational content to expand your knowledge and discover how our expertise can support your success.
Electrohydraulic solutions combine the precision of electronic control with the power of hydraulic systems, creating highly efficient components that power everything from construction equipment to industrial machinery. As original equipment manufacturers face increasing pressure to deliver superior performance while managing costs, these specialized systems have become essential for maintaining competitive advantage.
The challenge for OEMs isn't just finding hydraulic components—it's finding the right components that integrate seamlessly with existing systems while meeting strict quality standards and budget constraints. Generic, off-the-shelf solutions rarely deliver the performance optimization that custom applications demand.
The Strategic Advantages of Tailored Electrohydraulic Solutions
Increased Efficiency Through Precision Engineering
Custom electrohydraulic solutions are designed to meet specific application needs. Unlike off-the-shelf parts that require manufacturers to make compromises, these tailored systems provide the exact flow rates, pressure levels, and controls needed for performance..
This precision engineering translates directly to operational benefits. Equipment powered by custom-configured electrohydraulic systems typically operates 15-25% more efficiently than those using generic alternatives. The improved efficiency reduces energy consumption, minimizes heat generation, and extends component life cycles.
For OEMs, this means delivering equipment that performs better in the field while reducing warranty claims and maintenance requirements. The enhanced performance also provides a competitive differentiator when bidding for contracts or competing in price-sensitive markets.
Long-Term Cost Savings Through Strategic Customization
While tailored electrohydraulic solutions may require higher initial investment compared to off-the-shelf alternatives, the total cost of ownership typically decreases significantly over the equipment's operational life. Custom components eliminate the need for costly modifications, adapters, and workarounds that generic solutions often require.
The cost benefits extend beyond component pricing. Custom solutions reduce assembly time during manufacturing, minimize inventory complexity, and decrease the likelihood of field failures. These operational improvements directly impact production costs and profitability.
OEMs working with specialized electrohydraulic partners also benefit from consolidated sourcing arrangements. Rather than managing multiple suppliers for different components, manufacturers can streamline their supply chains while maintaining quality standards and delivery schedules.
Enhanced Reliability Through Application-Specific Design
Reliability represents a critical factor for OEMs, particularly those serving demanding industries like construction, mining, and industrial manufacturing. Custom electrohydraulic solutions address specific environmental conditions, duty cycles, and performance requirements that generic components may not withstand.
Application-specific design considers factors such as operating temperature ranges, contamination levels, vibration exposure, and maintenance access. Components engineered for these specific conditions demonstrate superior reliability and longer service life compared to generic alternatives.
This enhanced reliability reduces warranty costs, minimizes field service requirements, and strengthens customer relationships. OEMs can confidently specify longer warranty periods and reduce service network requirements when equipment incorporates properly engineered custom components.
Bailey International's Collaborative Approach to Custom Solutions
Partnership-Driven Design Process
Bailey International's approach to custom electrohydraulic solutions emphasizes collaborative engineering partnerships with OEMs. Rather than simply supplying components, Bailey's technical team works directly with manufacturers to understand application requirements, environmental conditions, and performance objectives.
This partnership approach begins during the design phase, where Bailey's engineers collaborate with OEM design teams to optimize component specifications and integration requirements. The collaborative process ensures that custom solutions integrate seamlessly with existing systems while meeting all performance and quality standards.
The partnership extends beyond initial design to include ongoing support throughout the product lifecycle. Bailey provides technical assistance for field applications, troubleshooting support, and component optimization recommendations based on real-world performance data.
Comprehensive Customization Capabilities
Beyond standard component configuration, Bailey offers complete system customization including cylinders, power units, and control systems engineered for specific applications. These comprehensive solutions address complex integration challenges that individual components cannot solve.
Custom Cylinders: Engineered solutions using high-grade materials and precise manufacturing processes to meet exact application requirements. Bailey's cylinder customization includes bore sizes, stroke lengths, mounting configurations, and seal selections optimized for specific operating conditions.
Power Units: Complete hydraulic power systems designed for seamless integration with OEM equipment. Customization options include pump selection, reservoir sizing, filtration systems, and control interfaces tailored to application requirements.
Control Systems: Application-specific control solutions powered by our Sure Grip Controls brand, providing precise system control. Custom control solutions integrate seamlessly with existing equipment architecture while providing enhanced functionality and reliability.
Real-World Applications and Success Stories
Heavy Equipment Simulation Training
CM Labs Simulations, a global leader in heavy equipment simulation training, required specialized electronic throttle components for their simulator systems. The standard Sure Grip Controls 10459 Floor Electronic Throttle provided the foundation, but needed specific modifications to meet their exacting requirements.
Bailey's technical team collaborated with CM Labs to modify the throttle component, addressing precise functional requirements while maintaining the reliability and performance standards essential for training applications. The customized solution integrated seamlessly with CM Labs' Edge Series simulators, enhancing performance and user experience.
This three-year partnership demonstrates how collaborative engineering approaches deliver superior results compared to standard component sourcing. The ongoing relationship has enabled continuous improvement and optimization based on real-world performance data.
Industrial Manufacturing Applications
Bailey serves diverse industrial applications, including oil and gas, marine, material handling, and manufacturing equipment. Each industry presents unique challenges requiring specialized solutions.
For oil and gas applications, Bailey provides components engineered for harsh environmental conditions, including extreme temperatures, corrosive environments, and high-vibration applications. Marine applications require components resistant to saltwater corrosion while maintaining precise control in challenging sea conditions.
Material handling equipment demands components that provide smooth, precise control for operator safety and productivity. Bailey's customized solutions address these specific requirements while maintaining the reliability essential for industrial applications.
Maximizing Value Through Strategic Partnerships
Technical Expertise and Support
Bailey's technical expertise extends beyond component manufacturing to include comprehensive engineering support throughout the product lifecycle. This support includes system design consultation, component selection optimization, and field application assistance.
The technical team provides training resources, including specialized sessions that help OEM teams understand component capabilities and optimization opportunities. This educational approach ensures that manufacturers can maximize the value of their custom electrohydraulic solutions.
Ongoing technical support includes troubleshooting assistance, performance optimization recommendations, and component upgrade paths as technology evolves. This comprehensive support approach strengthens the partnership relationship while ensuring long-term success.
Supply Chain Reliability and Flexibility
Bailey maintains extensive inventory and in-house manufacturing capacity to ensure reliable delivery schedules. This supply chain strength enables OEMs to maintain production schedules even when facing urgent requirements or unexpected demand changes.
The company's distribution network, including strategically located warehouses, provides rapid response capabilities for both standard and custom components. This logistics infrastructure supports OEMs' need for flexible, reliable supply chain partnerships.
Bailey's supply chain approach also includes demand forecasting and inventory optimization services that help OEMs reduce carrying costs while maintaining service levels. These value-added services demonstrate the comprehensive nature of Bailey's partnership approach.
Strategic Implementation for OEMs
Assessment and Planning
Successful implementation of tailored electrohydraulic solutions begins with comprehensive assessment of current applications, performance requirements, and cost objectives. OEMs should evaluate existing component performance, identify optimization opportunities, and establish clear success metrics.
The assessment process should include analysis of total cost of ownership, including initial component costs, installation requirements, maintenance needs, and expected service life. This comprehensive evaluation ensures that custom solutions deliver genuine value compared to alternatives.
Planning should also consider supply chain implications, including sourcing consolidation opportunities, inventory optimization, and logistics coordination. These strategic considerations maximize the benefits of custom electrohydraulic solutions.
Partner Selection and Collaboration
Choosing the right electrohydraulic solutions partner requires evaluation of technical capabilities, manufacturing capacity, and service approach. OEMs should prioritize partners with demonstrated experience in their specific industries and applications.
The collaborative relationship should begin during the evaluation phase, with potential partners providing technical consultation and preliminary design recommendations. This early collaboration helps establish the partnership foundation while ensuring alignment on technical requirements and expectations.
Ongoing collaboration includes regular performance reviews, optimization assessments, and strategic planning sessions. These partnership activities ensure continuous improvement and adaptation as requirements evolve.
Building Your Competitive Advantage
Tailored electrohydraulic solutions represent more than component customization—they provide strategic advantages that strengthen competitive positioning, reduce operational costs, and enhance customer satisfaction. OEMs that embrace custom solutions gain flexibility, reliability, and performance advantages that generic alternatives cannot match.
The key to success lies in establishing collaborative partnerships with experienced electrohydraulic solutions providers who understand your industry requirements and can deliver comprehensive support throughout the product lifecycle. These partnerships enable continuous improvement and innovation while ensuring reliable supply chain performance.
Bailey International's comprehensive approach to custom electrohydraulic solutions provides OEMs with the technical expertise, manufacturing capabilities, and partnership commitment necessary for long-term success. From rapid component customization through complete system engineering, Bailey delivers solutions that enhance equipment performance while reducing total cost of ownership.
Explore how tailored electrohydraulic solutions can benefit your team today.
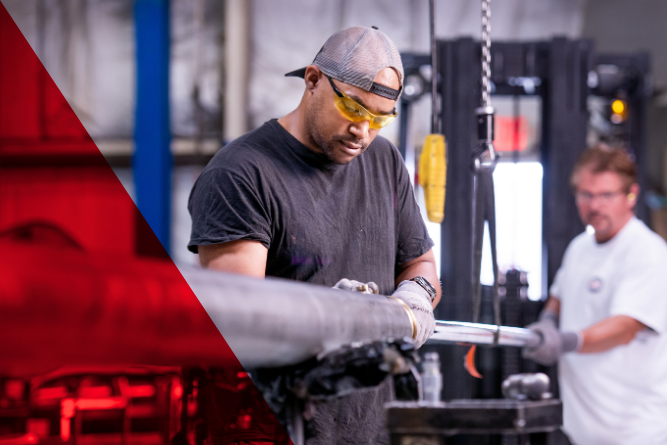
Why Tailored Electrohydraulic Solutions Are Game-Changers for OEMs
For over 45 years, Bailey International has set the standard for engineering excellence in mobile hydraulics. As a trusted industry leader, Bailey designs and manufactures hydraulic power units that serve as the driving force behind the most demanding applications. Our unwavering commitment to quality and innovation ensures that every power unit delivers optimum performance, reliability, and durability.
The Foundation of Every Hydraulic System
A hydraulic power unit is the core of any hydraulic system—responsible for transforming fluid power into controlled, mechanical force. Bailey International’s units consistently deliver the precision and strength required by professionals in agriculture, transportation, construction, and manufacturing.
Each Bailey hydraulic power unit is engineered with three essential components:
- Motor: Initiates the system with dependable power and consistent rotation.
- Pump: Ensures reliable fluid movement and system efficiency.
- Valve: Provides precise control, directing hydraulic fluid exactly where needed.
Every Bailey hydraulic power unit is built to exacting standards, offering flexibility and superior performance across a vast range of configurations.
Tank
The tank is engineered to safely store hydraulic fluid, with capacities ranging from 0.5 gallons to over 1,000 gallons. Bailey offers meticulous sizing to meet your specific operational requirements.
Pump
Our pumps are designed for seamless operation inside the tank, providing optimal suction and maximizing system longevity. Each pump is selected to fit the unique flow and pressure needs of your application.
Valve Options
Bailey provides an extensive selection of valve types, each manufactured for superior control and robust service life. Our valves activate work ports that efficiently power cylinders, jacks, and steering mechanisms.
Motor
Bailey’s catalog includes a broad spectrum of motors to meet any need:
- DC Motors
- AC Motors
- Hydraulic Motors
Each motor is engineered to deliver efficient and reliable performance in your specific application. Our DC motors are designed for use in mobile and industrial equipment, with options for low voltage/high torque or high voltage/low speed applications. AC motors are available in both single and three phase options, suitable for a wide range of agricultural, construction, and material handling equipment. For heavy-duty machinery requiring precise control and smooth operation, our hydraulic motors offer superior performance.
Discover the perfect solution for your needs by contacting our team of experts to discuss your requirements or request a quote. Together, we can power the success of your next project!
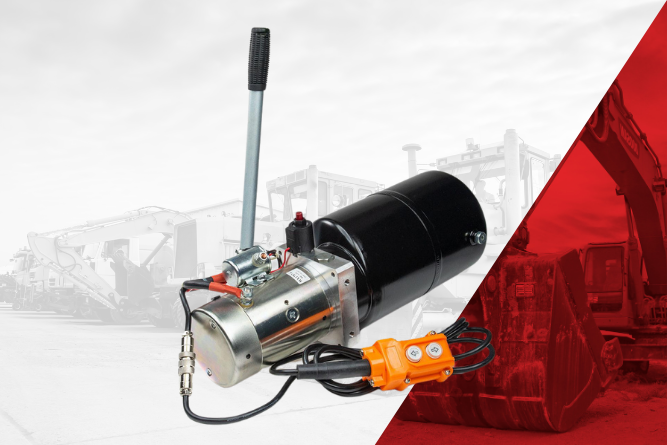
Hydraulic Power Unit Basics
The fluid power industry, like many others, is facing challenges due to the recent global economic slowdown. For OEMs who rely on hydraulic components, this downturn emphasizes the need to adapt quickly to stay competitive, maintain profitability, and drive growth.
To help your business navigate the slowdown, we’ve outlined four key strategies to build resilience, boost efficiency, and position your company for long-term success.
Diversify Product Offerings for Market Longevity
Diversifying your product lineup has never been more important. Expanding your offerings can reduce risks from market fluctuations and help you stay competitive in evolving industries. Here’s how you can future-proof your business:
- Consider Adding Electronic Controls to Your Products: Integrating electronic controls into your product lineup is a smart way to keep up with the growing demand for electro-hydraulic systems in mobile markets. By offering high-efficiency control solutions like precision flow valves and customized controls, you can attract a wider customer base while staying ahead of the shift toward automation.
- Focus on Energy-Efficient Systems: Sustainability is a major focus for industries like agriculture and construction, which are under pressure to meet environmental goals. Energy-efficient solutions, such as high-efficiency hydraulic pumps, can help your business cater to these needs while positioning you as a leader in the green technology market.
By offering innovative solutions, you’ll tap into new market segments and reduce reliance on traditional products. Diversifying your product lineup ensures your business stays competitive, even as market demands change.
Enhance Customer Service to Cultivate Loyalty
Exceptional customer service is the key to building strong business relationships, especially during challenging times. Here are three proven strategies to improve customer retention and satisfaction:
- Provide Expert Technical Support: Help your customers get the most out of your products with tailored technical support. Equip your team with product training and updated technical guides, so they can quickly troubleshoot issues and optimize system performance. By offering personalized assistance, you add value to every interaction.
- Stay Proactive with Communication: Keep your customers informed by anticipating their needs. Send restocking notifications, reminders for maintenance contracts, or updates on new products and services. Proactive communication builds trust and creates a lasting partnership.
- Ensure Faster Turnaround Times: Reduce delays and improve customer satisfaction by streamlining your processes. Offer fast shipping options, such as 2-day delivery, to get your products to customers quickly and efficiently.
By focusing on technical expertise, proactive engagement, and fast service, your business establishes itself as a reliable partner. Prioritizing customer service not only improves retention, but also helps you stand out in a competitive market.
Upskill Your Workforce
A business downturn is the perfect time to focus on workforce development. By upskilling your employees, you can foster innovation, stay competitive, and adapt to changing market demands. Here are three key strategies to invest in your team:
- Cross-Training Programs: Cross-training employees enhances operational flexibility and promotes team collaboration. Cross-trained teams are better equipped to solve problems across departments, leading to faster decision-making and improved efficiency.
- Industry-Specific Certifications: Encourage your employees to earn certifications relevant to your industry. Certified staff can provide expert insights and tailored recommendations, improving customer satisfaction and building trust.
- Workshops on Emerging Technologies: Stay ahead of the curve by offering training in artificial intelligence (AI), machine learning, and the Internet of Things (IoT). Employees skilled in these technologies can create innovative solutions that meet evolving customer needs and market trends.
Upskilling your workforce is an investment in your business's future. Equip your team with the tools they need to succeed, and you’ll be ready to face any challenge.
Focus on Operational Efficiency
Reducing overhead costs without sacrificing quality is key to maximizing profit margins. To help you run your business more efficiently, here are two proven ways to streamline operations:
- Optimize Inventory Management: Use predictive inventory management software to keep your shelves stocked with best-selling items, while avoiding excess inventory of slow-moving products. This strategy minimizes waste and saves money, helping boost productivity and cut costs.
- Leverage Data-Driven Decision Making: Rely on real-time data from advanced ERP (enterprise resource planning) systems to monitor expenses, track performance metrics, and identify areas for improvement. By using data effectively, you can improve operational efficiency and reduce unnecessary business costs.
Implementing these strategies will help you increase profitability while maintaining high-quality operations.
Building a Resilient Future
Navigating changes in the fluid power market requires adaptability, innovation, and strategic planning. To stay ahead during a slowdown, businesses can focus on diversifying product lines, strengthening customer relationships, upskilling employees, and streamlining operations. These strategies not only help overcome challenges, but also prepare your business for strong growth when the market recovers.
At Bailey International, we are more than just a hydraulic components supplier—we’re your trusted partner in growth. We specialize in providing high-quality hydraulic components, custom hydraulic solutions, and expert support tailored to meet the unique needs of OEMs and businesses in the fluid power industry.
Whether you’re searching for durable hydraulic cylinders, hydraulic pumps, or custom engineering, our team is here to help you succeed. Let us support your profitability and adaptability in this ever-changing market.
Contact Bailey International today to explore reliable, cost-effective solutions that drive your business forward.
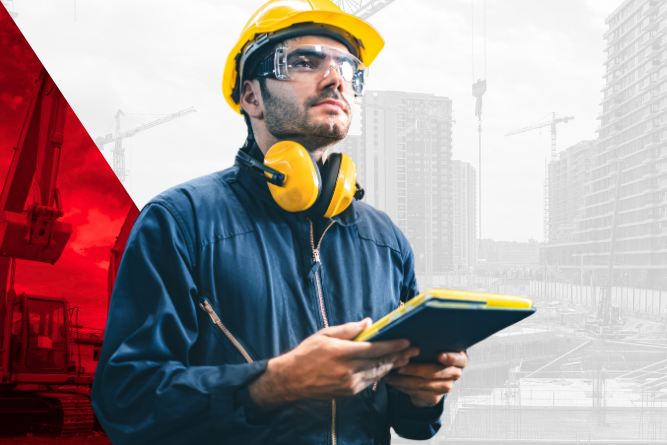
4 Ways to Combat Market Slowdown
A hydraulic system is a closed system that converts pressurized fluid to mechanical energy. Hydraulic fluid is moved by pumps through control valves and on to mechanical actuators like hydraulic cylinders or motors, which then use the pressure to move implements such as tractor buckets, excavators, and lift cranes.
Components of a Hydraulic System
A hydraulic system is composed of various components to keep the fluid under the desired pressure, clean, and moving in the right direction. Below is an overview of those components
Reservoir Tank
The hydraulic tank acts as a reservoir, holding fluid, and is connected directly to the pump. It allows air bubbles to dissipate and contamination particles to settle, as well as allows the oil to cool while it is not circulating. A vented filter cap controls air flow, and a filter or strainer keeps contaminants out of the hydraulic fluid.
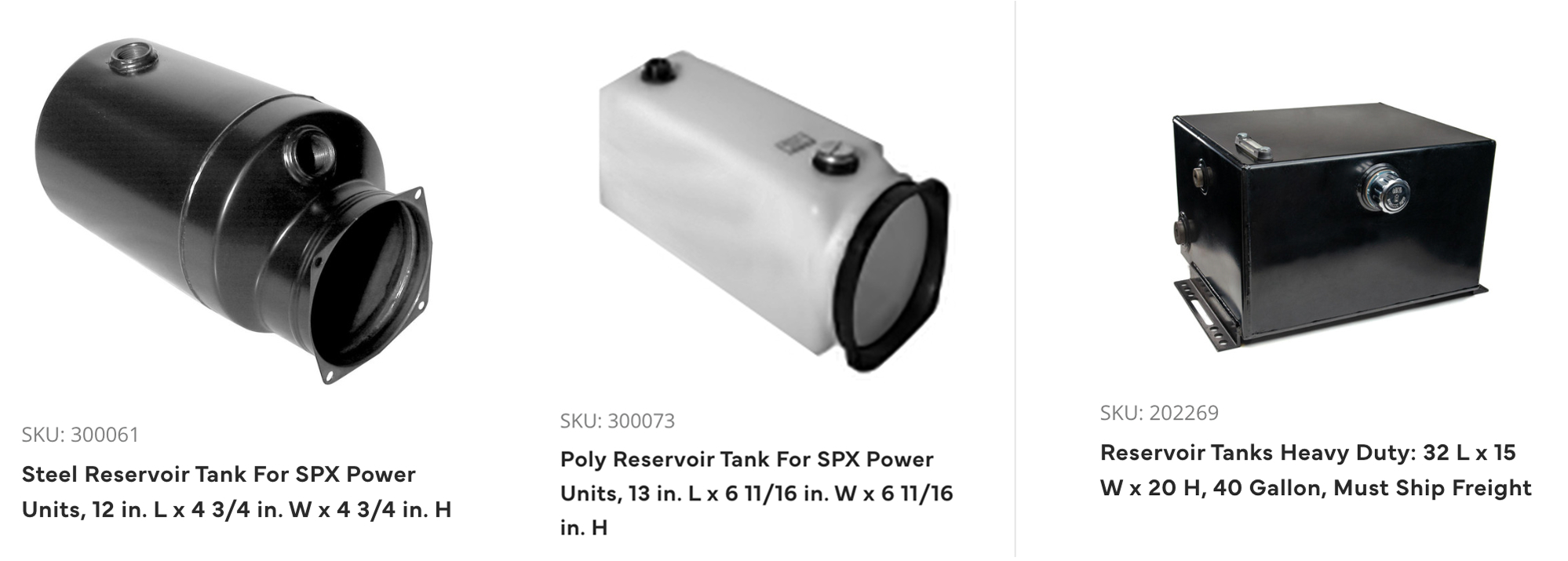
Pump and Engine
The hydraulic pump moves liquid from the reservoir tank through the system driven by an engine. Pump designs are typically two-stage, PTO or manual hydraulic, while the engine can be gas, diesel or electric depending on access to power, the horsepower needed and mounting style.
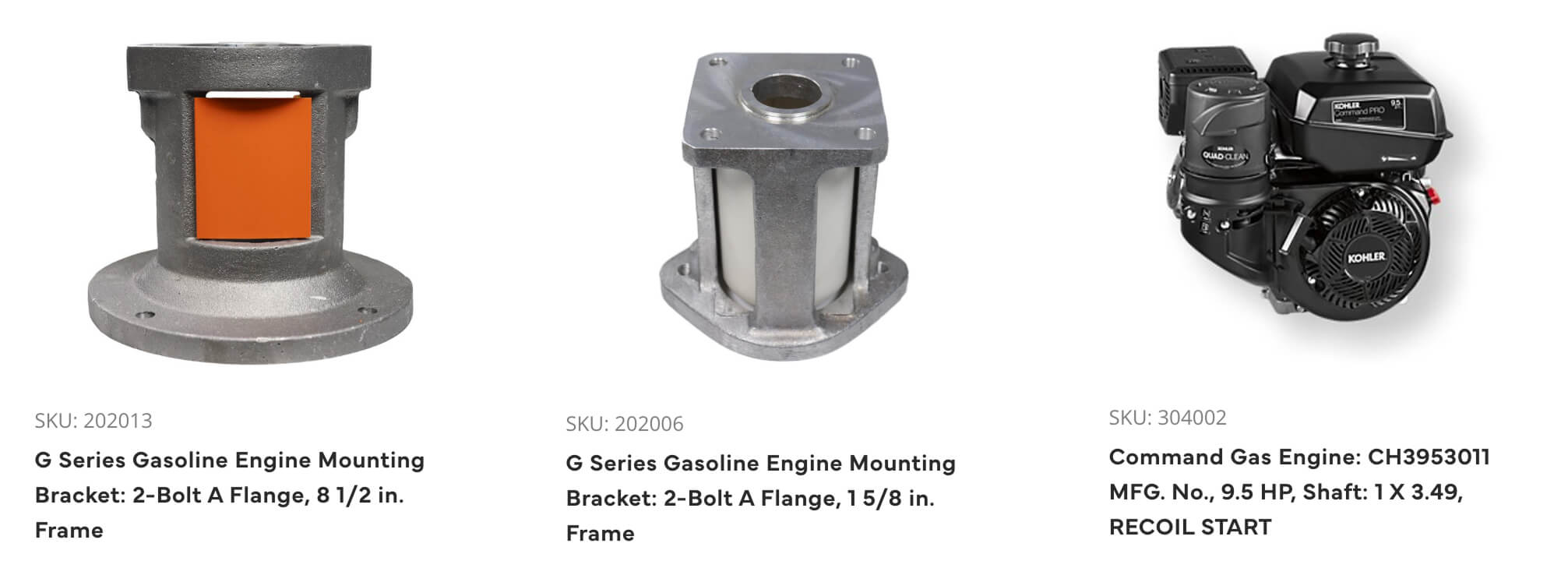
Pressure Gauges and Relief Valve
Once liquid is circulating, gauges can be used virtually anywhere in the system to monitor pressure. In addition, a relief valve controls the fluid pressure that powers the hydraulic cylinder; excess fluid is returned to the reservoir tank. This prevents pressure build-up and potential damage to equipment.
Valve Assembly
The hydraulic valve assembly controls the direction, pressure and flow rate of fluid through a hydraulic circuit. It regulates the speed of motors and movement of cylinders. Directional control valves are most common, controlling fluid flow from the pump to the cylinders and other system components.
Cylinder
A hydraulic cylinder is an actuator that creates linear movement by converting hydraulic energy back to a mechanical movement – so it is the component that drives the work performed by mobile equipment. Cylinders can be used to lift, push, pull and press loads that require exceptional force.
Motor
Similar to cylinders, motors are actuators that converts hydraulic pressure and flow into movement, but it’s converted into torque and angular displacement (rotation) rather than linear motion. The amount of pressure and displacement of a motor will determine how much torque is produced while the amount of flow will determine the speed.
Flow Control Valve
The purpose of a flow control valve is to regulate the flow rate to motors and cylinders, thereby regulating the speed of those components.
Fluid Cooler
This unit removes the excess heat generated from the hydraulic fluid and helps to keep the temperature within a limited range before returning to the reservoir. Without proper cooling, the hydraulic system could overheat, causing component damage. Keeping the system properly cooled also extends hydraulic fluid life.
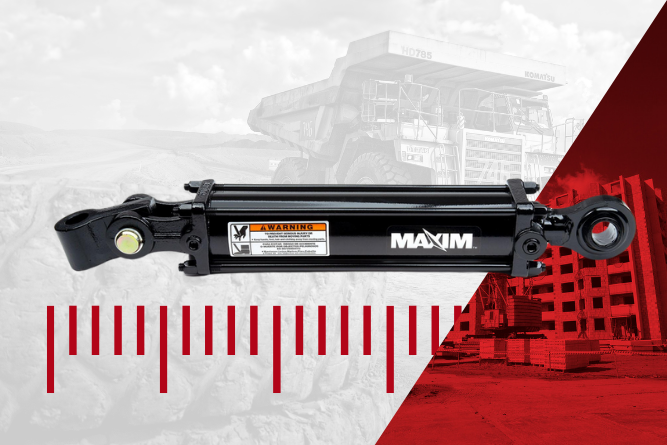
How Does A Hydraulic System Work?
A hydraulic cylinder is made up of a steel barrel, a piston connected to a piston rod that moves back and forth, and mounting accessories. A cylinder creates linear movement by converting hydraulic energy back to a mechanical movement. They are used in equipment to lift, push, pull and press loads that require exceptional force.
Hydraulic cylinders can be double-acting (pressurized oil moves it in either direction) or single-acting (pressurized oil extends the rod in one direction, and gravity pushes it back to its natural position).
To properly select a cylinder there are several factors to consider:
- Bore size (tube diameter) which determines how much force can be delivered at a given oil pressure
- Stroke, or how far the rod extends
- Piston rod diameter which is critical since it must apply that force without bending or buckling
- Speed determines the gallons per minute needed from the hydraulic pump and determines the correct port sizes
- How the cylinder will mount
We have hydraulic formulas and hydraulic calculators to make sure your cylinder is sized properly for the application. We at Bailey International are your trusted source for hydraulic products, system design help, as well as education and general support. After the sale, it’s the service and support that count!a
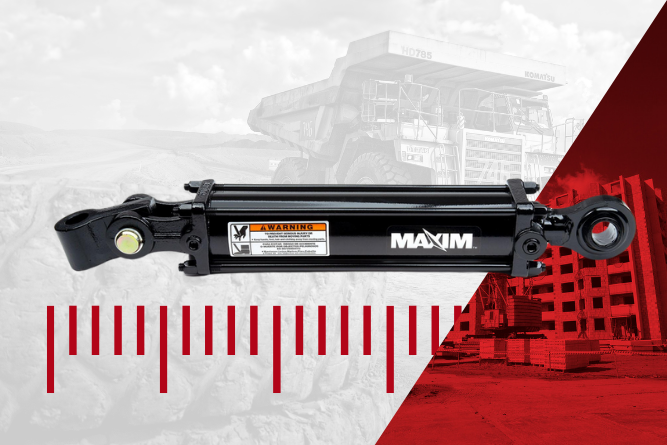
What is a Hydraulic Cylinder?
There are different types of hydraulic cylinders available that are designed to work within specific applications. Below is a brief explanation of the most common cylinder types along with some specialty cylinders that are available from Bailey.
The Basics
A hydraulic cylinder is an actuator that creates linear movement by converting hydraulic energy back to a mechanical movement. Cylinders are made up of a steel barrel, a piston connected to a piston rod that moves back and forth, and mounting accessories. They are used in equipment to lift, push, pull and press loads that require exceptional force.
Available in several different body styles, including tie-rod, welded and telescopic, hydraulic cylinders can be single-acting or double-acting.
Single-acting cylinders vs double-acting cylinders
Single-acting Cylinders
In a single acting hydraulic cylinder, piston force is applied in a single direction when pressurized oil extends the rod. Once the oil is exhausted, gravity and the load return it to its natural position.
Double-acting Cylinders
Double-acting cylinders can exert force in two directions. The piston cylinder is divided into two pressurized chambers that enable the rod to achieve both outward and return strokes. Pressurized oil allows the rod to move in either direction.
So how do you choose between single-acting and double-acting? Single-acting cylinders are best for simpler applications, where you only need to push in one direction. Double-acting cylinders are more complex to operate and maintain but offer both push and pull forces, have more precise control, and are better for repetitive actions.
Basic Body Styles
Tie-Rod Cylinders
Tie-rod hydraulic cylinders use high strength threaded steel rods to hold the two end caps to the cylinder barrel. They are held together by four or more threaded tie bolts that run the length of the entire cylinder tube. These bolts hold the baseplate and head together. They usually have static seals to prevent leakage between the barrel and end-cap interface. Tie-rod cylinders are best for medium to light-duty mobile applications. Their cost of ownership is lower, since they are easier to assemble, maintain and repair.
Standard Tie-rod Cylinder
Rephasing Tie-rod Cylinder
Rephasing tie-rod cylinders incorporate an internal bypass for synchronizing the cylinder in a series circuit. They are ideal for construction and agricultural applications where you need to lift independent loads plumbed in series.
Welded Cylinders
In a welded hydraulic cylinder, the barrel is welded to the end caps rather than using steel rods. Static seals are used to seal the head or gland of a welded cylinder. Welded body cylinders have many advantages over tie-rod cylinders, including a compact design that usually can withstand higher pressures, often greater than 5,000 psi. Because of this, they are often used on mobile machinery where space is at a premium. Their rugged design not only makes them ideal for extreme weather and operating conditions, but also contributes to much longer service life than tie-rod cylinders because they do not fail due to tie-rod stretch at high pressures and long strokes.
Telescopic Hydraulic Cylinders
Telescopic cylinders are several individual cylinders (like the sections of a telescope) nested together in order of decreasing size. Because this style of cylinder is able to extend from its compact design, it provides an exceptionally long stroke. The collapsed length of a typical telescopic cylinder varies between 20% to 40% of its extended length. In general, telescopic cylinders are single acting and are available in two to five stages. They are frequently used in trucks in the construction industry, vehicle trailers, garbage and dump trucks, as well as in the agricultural industry.
Bailey Specialty Cylinders
Chief AT
The Chief® AT line of cylinders is a durable alternative to tie-rod cylinders for lighter duty construction and agriculture applications. Unlike a tie-rod, there are no bolts. They feature an easy snap ring on the rod-end gland for easy field repair.
Chief WX
The Chief® WX line of cylinders features patented designs and is ideal for applications where port adjustability and overall cylinder space is restricted. It features an adjustable 360° rotating gland with retaining ring design offering 2 base-end ports for applications requiring a variety port positions.
Chief WTG
The Chief® Welded Tang cylinder, or WTG for short, features Bailey's patented adjustable 360° rotating gland and is one of our most durable cylinders. It is sometimes referred to as a lug end cylinder, due to its one piece lug mount welded to both the rod and base ends. The WTG can utilize a spherical ball or steel bushing insert to improve wear life. Tang cylinders are commonly used in heavy duty construction equipment.
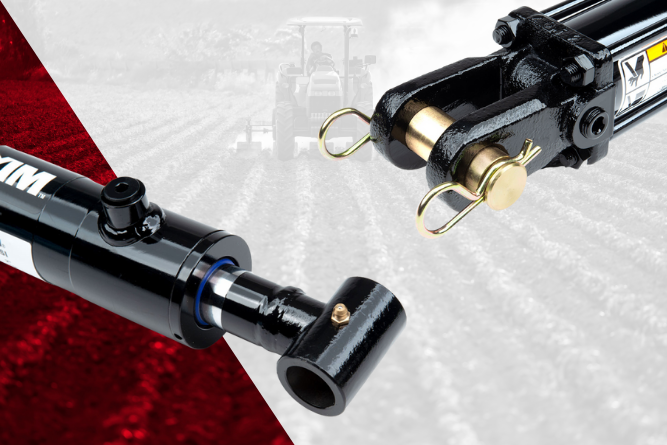
Types of Hydraulic Cylinders
Like any mechanical component, hydraulic pumps are prone to failure if not carefully maintained. With proper understanding and attention, you can not only prevent these failures but also extend the life of your hydraulic system significantly.
The Common Causes of Hydraulic Pump Failure
Despite their robust design, hydraulic pumps are vulnerable to specific challenges. Improper system maintenance or design issues can lead to one or more of the following problems:
1. Excess Heat
One of the most common culprits of hydraulic pump failure is heat. Hydraulic systems naturally generate heat during operation. While some heat is normal, too much can be detrimental. If left unaddressed, excess heat can cause significant damage to seals, valves, and other system components.
Why Is Heat an Issue?
High oil temperatures break down hydraulic fluids, reducing their viscosity and causing inadequate lubrication. Over time, this leads to increased wear and tear on the pump and other components. Additionally, heat can cause seals to harden or deteriorate, leading to oil leaks and eventual system failures.
How to Prevent Excess Heat
- Proper Reservoir Size: Ensure the oil reservoir is adequately sized for the system’s operating conditions. A well-sized reservoir allows for better heat dissipation.
- Install Oil Coolers: Adding an oil cooler to your system can help keep hydraulic fluid temperatures within acceptable levels.
- Monitor Fluid Levels Regularly: Insufficient oil levels can cause the system to overheat. Always maintain adequate oil levels and top off when necessary.
2. Contamination
Contamination within the hydraulic system is another leading cause of pump failure. This can occur when dirt, debris, or other foreign particles enter the system.
Why Is Contamination Dangerous?
Contaminants can damage the pump's internal components, such as pistons and gears, reducing efficiency and causing wear. They can also block vital system pathways, further straining the pump and other hydraulic components.
How to Prevent Contamination
- Regularly Change Filters: Use proper filtration systems and change filters at regular intervals to keep the hydraulic fluid clean.
- Use High-Quality Hydraulic Fluids: Poor-quality or incompatible hydraulic fluids can introduce foreign substances. Always use the recommended fluid type for your system.
- Inspect and Maintain Seals: Worn-out seals can allow contaminants to enter the system. Regular inspection and replacement of seals help prevent this issue.
3. Cavitation
Cavitation occurs when there is insufficient flow of hydraulic fluid to the pump’s inlet. This creates voids or air bubbles within the fluid, which collapse under pressure, damaging pump components.
Signs of Cavitation
One telltale sign of cavitation is foamy hydraulic oil. This indicates air is entering the system. Other symptoms include unusual noise during operation or a decrease in pump efficiency.
How to Prevent Cavitation
- Increase the Size of the Inlet Line: A larger inlet line can improve the flow of hydraulic fluid to the pump.
- Avoid Elbows and Bends: Remove any unnecessary elbows, bends, or filters on the inlet line to ensure a smoother flow of hydraulic oil.
- Position the Reservoir Above the Pump: Having the oil reservoir located above the pump helps maintain a steady flow and reduces the likelihood of cavitation.
Prolonging the Life of Your Hydraulic Pump
Preventing pump failure starts with proper system design and consistent maintenance practices. Here are additional tips to maximize the lifespan of your hydraulic pump:
- Monitor Oil Quality and Temperature: Regularly check the oil temperature and quality to detect early signs of heat-related issues or contamination.
- Schedule Routine Inspections: Periodically inspect the system components for wear, leaks, and signs of damage. Early detection can save you thousands in repairs and downtime.
- Implement Predictive Maintenance: Use advanced diagnostic tools to identify potential issues before they escalate. Many modern hydraulic systems now include sensors that monitor performance in real-time.
Partnering with a Reliable Source for Hydraulic Components
When it comes to maintaining and repairing hydraulic systems, the quality of your components matters. Low-quality parts not only wear out quickly but can also introduce new vulnerabilities to your system. That’s where trusted experts like Bailey International can make a difference.
With over 40 years of expertise in hydraulic components, Bailey International provides reliable, high-quality solutions tailored to your industry’s needs. From hydraulic pumps to filters, their extensive range of products and expert support ensures your system operates at its best.
Why Choose Bailey International?
- Experience You Can Trust: With decades of experience, Bailey has become a trusted partner for construction professionals, hydraulic engineers, and mechanics.
- Custom Solutions: For unique operational needs, Bailey offers customized components through its MVP program.
- Comprehensive Support: Bailey provides expert guidance every step of the way, from design to maintenance.
Looking to optimize your hydraulic systems even further? Take advantage of Bailey International’s vast catalog of hydraulic components and extensive expertise. Whether you need routine maintenance supplies or custom solutions, they’ve got you covered. Visit our digital catalog today and discover how Bailey can power your progress.
_thumbnail.jpg)
Why Hydraulic Pumps Fail (And How to Prevent It)
Hydraulic cylinders are a critical component in countless industries, from construction and oil & gas to agriculture and manufacturing. Among the most common types of hydraulic cylinders are tie rod cylinders and welded cylinders, both of which excel in different applications.
If you're looking to choose between the two, understanding their construction, advantages, and ideal use cases is essential. This guide breaks down the key differences between tie rod and welded cylinders, so you can make informed decisions for your operations.
What is a Tie Rod Cylinder?
A tie rod cylinder is a type of hydraulic cylinder held together using high-strength steel tie rods. The rods run the length of the cylinder, keeping the baseplate and gland secured.
Key Features of Tie Rod Cylinders:
- Easily Repairable
These cylinders are built to be disassembled efficiently, making them simple to repair and maintain in the field. With just a wrench, you can remove the tie rods, open the cylinder, and service its internal components.
- Compact Design for Specific Applications
Tie rod cylinders are generally found in applications where space is constrained and the cylinder size needs to remain standard.
Ideal Use Cases:
Tie rod cylinders are most commonly found in:
- Industrial machinery
- Food processing equipment
- Medical devices like hospital beds
If your operation involves controlled environments or predictable loads, tie rod cylinders often fit the bill perfectly.
What is a Welded Cylinder?
Unlike tie rod cylinders, a welded cylinder relies on a single, sealed construction. The end caps are welded directly to the body of the cylinder, eliminating the need for tie rods altogether.
Key Features of Welded Cylinders:
- Durable and Compact Design
Welded cylinders offer a sturdy and sleek design, which is particularly advantageous in demanding, high-pressure applications. They can endure higher stress and loads compared to tie rod cylinders.
- Requires Specialized Tools for Repairs
Repairing welded cylinders typically requires a vise grip and spanner wrench for gland removal. This makes fixing them slightly more technical than tie rod cylinders.
Ideal Use Cases:
Welded cylinders are designed for heavy-duty environments such as:
- Construction equipment (e.g., excavators, loaders)
- Farming machinery
- Oil & gas applications where rugged durability is essential
Their compact design and high reliability make them a preferred choice for mobile equipment.
Key Differences Between Tie Rod and Welded Cylinders
1. Construction
- Tie Rod Cylinders: Held together by external tie rods, making them easier to disassemble.
- Welded Cylinders: Features a seamless body with welded ends for added durability.
2. Maintenance and Repair
- Tie Rod Cylinders: Easier to repair in the field with basic tools.
- Welded Cylinders: Require more advanced tools and technical expertise for maintenance.
3. Durability
- Tie Rod Cylinders: Better suited for lower pressure and controlled applications.
- Welded Cylinders: Can endure higher pressure and are built to withstand more rugged environments.
4. Application Suitability
- Tie Rod Cylinders: Best for stationary, indoor applications with predictable conditions.
- Welded Cylinders: Ideal for mobile, heavy-duty operations with high performance demands.
5. Cost
- Tie Rod Cylinders: Tend to be more cost-effective and easier to replace due to simple construction.
- Welded Cylinders: Slightly more expensive upfront but offer long-term reliability for extreme conditions.
Which Cylinder Should You Choose?
The choice between a tie rod cylinder and a welded cylinder ultimately depends on your application and priorities. Here’s a quick comparison to help you decide:
- Tie Rod Cylinder: Tie rod cylinders are easy to maintain with basic tools. They are durable in controlled conditions and cost-effective, making them ideal for stationary, industrial applications.
- Welded Cylinder: Welded cylinders are more durable and designed for high-pressure, rugged environments. Maintenance requires specialized tools, and they have a higher upfront cost, making them perfect for mobile and heavy-duty applications.
If you're working in environments that require extensive field maintenance, like a factory floor, tie rod cylinders are your best bet. However, if your equipment operates in tough conditions—such as construction sites or oil fields—welded cylinders are designed to handle the pressure.
Why Choose Bailey for Your Hydraulic Cylinder Needs?
Bailey is a trusted leader with over four decades of expertise in hydraulics. Whether you're in construction, oil & gas, manufacturing, or agriculture, we provide top-quality hydraulic solutions you can rely on.
Here’s why professionals choose Bailey:
- Comprehensive Product Line: From tie rod cylinders to welded cylinders, we offer a wide range of standard and custom options.
- Expert Support: Need help finding the right cylinder for your application? Our engineering team is here to provide technical guidance.
- Reliable Delivery: With strategically located warehouses, we ship to most locations in just 2 days.
For more detailed specifications or to explore our hydraulic solutions, reach out to Bailey International today.
Not sure which cylinder suits your needs? Contact our team today to explore your options.
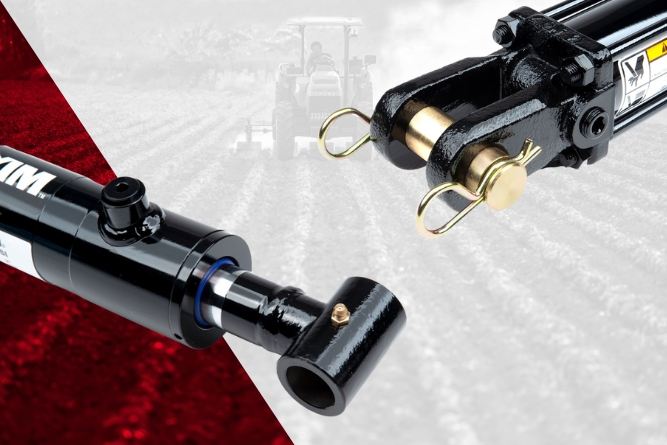
Tie Rod vs. Welded Cylinders: Which One is Right for Your Application?
What are custom manifolds, and how can they transform hydraulic systems? This blog post explores the role of custom manifolds in modern hydraulic applications, their benefits, and their importance to professionals like hydraulic engineers and construction specialists. Read on to learn more and discover how Bailey International's experts can help you optimize your systems.
What is a Hydraulic Manifold?
A hydraulic manifold provides pathways for the flow of hydraulic fluid within a system. It's a central component that distributes oil or fluid between pumps, actuators, cylinders, motors, and other parts. Instead of using multiple hoses or tubes, a manifold consolidates these pathways, ensuring seamless communication between components.
Manifolds can be simple in design, managing basic flow paths, or highly complex, controlling multiple operations simultaneously. The key to their performance is customization—tailoring the manifold to the specific needs of the system.
Simple Manifolds
A simple manifold, such as a relief manifold, connects basic elements of a hydraulic system. It features ports for pressure (P) and tank lines (T), and often houses a relief valve to manage pressure. For example, when system pressure exceeds a critical threshold, the relief valve opens, diverting excess fluid to prevent damage.
Complex Manifolds
Complex manifolds are engineered to execute more intricate functions, guiding hydraulic fluid through multiple pathways and managing multiple control valves. They enable systems to support advanced operations, such as running multiple actuators or pumps simultaneously.
Whether your system requires basic pressure management or intricate control across various components, custom manifolds simplify operations and improve efficiency.
Why Choose Custom Manifolds?
Custom manifolds are engineered to meet the exact specifications of a hydraulic system. But what sets them apart, and why should you consider custom solutions for your project? Here are some key reasons.
1. Streamlined Design
Instead of connecting numerous hoses or tubes, custom manifolds consolidate pathways into a single, compact unit. This leads to a cleaner design, reduced assembly time, and easier maintenance.
2. Enhanced Performance
By integrating custom manifolds into your systems, you achieve optimal flow paths, minimizing pressure drops and improving overall performance.
3. Space and Weight Savings
Custom manifolds are designed to fit seamlessly within your equipment, reducing the need for excessive tubing, fittings, and components. This leads to significant space and weight savings, which are critical in applications like mobile equipment and compact machinery.
4. Cost Efficiency
Over time, custom manifolds can reduce costs related to hose replacements, assembly, and potential downtime. Additionally, by consolidating multiple valves and components into one unit, your overall system becomes more cost-effective.
5. Improved System Reliability
Manifolds eliminate potential leak points caused by connecting hoses and fittings. Fewer connections mean fewer chances for failure, resulting in a more reliable system.
6. System Customization
Every hydraulic system has unique requirements. With custom manifolds, you get a solution built precisely for your system's flow rates, pressures, and operational needs.
Bailey International’s custom manifold solutions are designed to incorporate all these benefits while ensuring your hydraulic systems deliver consistent, high-performing results.
Manifolds in Action Across Industries
Manifolds aren't one-size-fits-all; the way they improve operations depends on the specific industry and system design. Let's take a closer look at a few examples.
Construction
Custom manifolds cater to the heavy-duty requirements of construction machinery, ensuring seamless operation of components like hydraulic cylinders and motors in excavators, loaders, and cranes.
Agriculture
For agricultural equipment like tractors or harvesters, custom manifolds manage hydraulic controls for precision farming techniques, such as adjusting implements and efficiently powering attachments.
Industrial Manufacturing
Manifolds enhance factory robotic systems by simplifying controls and improving fluid transfer, ensuring consistent performance in automated production lines.
Material Handling
Forklifts and stackers rely on custom manifolds to coordinate various hydraulic functions, including lifting mechanisms and steering controls.
Across these industries, custom manifolds provide more than fluid transfer—they streamline systems, maximize efficiency, and ensure equipment operates at its peak.
6 Steps to Designing a Custom Manifold
Creating a custom manifold tailored to specific system needs requires an expert-led, multi-step design process. Here’s an overview of the typical steps:
1. Understand Your System Needs
Work closely with hydraulic engineers to determine flow requirements, pressure ranges, operational functions, and compatibility with existing components.
2. Specify the Valves and Features
Identify the types of valves (e.g., relief valves or flow control valves) and any additional features you need, such as pressure-sensing capabilities or custom port configurations.
3. Develop the Design
Using advanced modeling software, our engineers design a manifold that incorporates your specifications. This ensures accuracy before manufacturing.
4. Prototype and Test
Next, our manufacturers develop prototypes and test them under operational conditions to ensure optimal performance and adherence to system requirements.
5. Build and Deliver
Once the prototype passes testing, the manifold is manufactured, quality-checked, and shipped for integration into your system.
6. Optimize and Maintain
With the manifold in place, periodic maintenance and optimization will ensure long-term system performance.
Bailey takes this approach to the next level, combining technical expertise and precise manufacturing to deliver custom manifold solutions that perform beyond expectations.
Get the Bailey Advantage
At Bailey, we understand the challenges hydraulic engineers and construction professionals face. That’s why we don’t just deliver parts—we provide solutions. With over 45 years of experience designing and manufacturing hydraulic systems, we work as your partner in creating efficient, reliable, and custom solutions.
With Bailey's custom solutions, you get:
- Tailored designs crafted by expert engineers
- Fast delivery, with most custom manifolds shipping in just a few weeks
- Comprehensive customer support throughout the design and implementation process
When you work with our team, you’re not just getting a product—you’re finding a collaborative partner invested in your success.
If you're ready to consolidate your system and optimize operations, Bailey's custom solutions are here to help. Contact our design team today to discuss your project and discover how we can build the perfect manifold for your needs.
Build smarter. Choose Bailey.
Get Started with Bailey Today
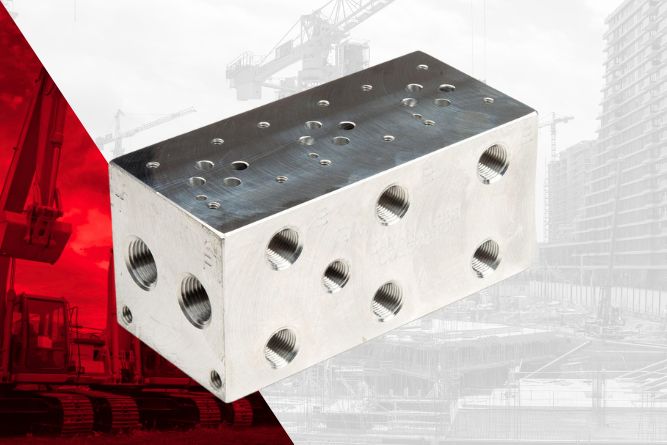
Custom Manifolds
Directional control valves are integral components in hydraulic systems, allowing precise management of fluid flow to perform various tasks. Whether you're designing a hydraulic system or troubleshooting one, understanding directional control valves can significantly improve system efficiency and functionality.
This guide dissects the essentials, applications, and types of directional control valves, providing insights tailored for hydraulic engineers and fluid power professionals.
What Are Directional Control Valves?
Directional control valves regulate the direction of hydraulic fluid in a system. By controlling the fluid’s flow path, these valves determine where energy will be transferred within the system, enabling tasks like lifting, turning, or pushing.
Their operation is based on controlling the spool inside the valve, which can be shifted to open or block specific flow paths.
Key Functions of Directional Control Valves:
- Start or stop fluid flow.
- Change the direction of fluid flow.
- Throttle flow to manage pressure and speed.
Types of Directional Control Valves
Directional control valves vary based on several factors, including the number of flow paths, spools, and their action or center type. Here are the most common classifications:
1. Based on Flow Paths
- 3-Way Valves: Have three ports—one pump line, one return line, and one work port. Commonly used in single-acting cylinders, these valves allow fluid flow in a simple circuit.
- 4-Way Valves: Add an extra work port, consisting of one pump line, one return line, and two work ports. Typically used in double-acting cylinders, these are more versatile and allow greater control over hydraulic flow.
2. Based on Positions
- 3-Position Valves: Feature forward, neutral, and reverse positions to handle dynamic fluid movement.
- 4-Position Valves: Include the same positions as three-position valves but add a flow position, enabling free movement of oil through open work ports.
3. Based on Spool Action
- Spring-Centered Spool Action: Automatically returns the valve to a neutral position when released. Ideal for applications requiring the valve’s default state to be inactive.
- Detent Spool Action: Locks the spool in place once moved, maintaining its set position until manually adjusted.
Special Application – Pressure Release Detent
One unique application is in log splitter control valves, which often include a pressure release detent. This allows the spool to spring back to neutral once a specific hydraulic pressure is reached, ensuring efficiency and safety.
4. Based on Center Type
- Tandem Center: Blocks work ports while allowing oil to flow freely back to the reservoir in neutral. Often used in mobile equipment.
- Open Center: Permits constant flow from the pump to the tank in neutral. Commonly paired with fixed-displacement pumps like gear pumps.
- Closed Center: Blocks all ports in neutral, ensuring no fluid flow. Typically paired with pressure-compensated pumps for applications requiring higher energy efficiency.
Why Are Directional Control Valves Critical in Hydraulic Systems?
The type of directional control valve you select directly impacts system performance. Faulty or incompatible valves can cause inefficiencies, reduced productivity, or even serious damage to components.
Benefits of Well-Chosen Directional Control Valves:
- Precision Control: Direct fluid flow with accuracy, ensuring tasks are performed seamlessly.
- Improved Efficiency: Leverage the right center type (tandem, open, closed) to minimize energy waste.
- Enhanced Safety: Safeguard systems from overpressure through specialized features like pressure release detents.
- Flexibility: Adapt to diverse equipment needs—whether for mobile construction machinery or industrial presses.
How to Choose the Right Directional Control Valve
Selecting the perfect valve involves evaluating the specific needs of your hydraulic system. Here is a structured approach:
1. Understand Flow Requirements
Determine the maximum flow rate your system demands and ensure compatibility with the valve’s capacity. Undersized valves create bottlenecks, while oversized valves can waste energy.
2. Match with Pump Design
Identify pump type—fixed displacement or variable displacement. Open-center valves are best suited to fixed pumps, while closed-center valves work well with variable pumps.
3. Opt for the Right Spool Action
Consider whether spring-centered (automatic return) or detent (manual locking) action is appropriate for your application.
4. Assess Pressure Ratings
Ensure the valve can handle the system's maximum pressure to sustain performance without risk of failure.
5. Account for System Layout
Examine how many work outputs you need to control. Choose between 3-way or 4-way valves based on single-acting or double-acting applications.
6. Prioritize Durability & Quality
Invest in valves from reliable manufacturers that provide robust warranties and technical support.
Applications for Directional Control Valves
Directional control valves are widely used across industries. Here are some examples:
- Agricultural Equipment: Precise control in plows, harvesters, and tillage machines.
- Construction Machinery: Seamlessly manage hydraulic arms in loaders and excavators.
- Material Handling: Govern fluid flow in forklifts and pallet trucks efficiently.
- Industrial Presses: Regulate hydraulic energy in metal forming processes.
- OEM Custom Designs: Adapt solutions to meet unique machine specifications across any industry.
Ensuring System Longevity with Proper Maintenance
Even the best valves require ongoing maintenance for long-term reliability. Follow these best practices:
- Frequent Inspections: Check for leaks, damaged seals, or debris in ports.
- Regular Cleaning: Ensure clear flow paths by removing any contaminants.
- Lubrication: Maintain smooth operation by keeping internal components adequately lubricated.
- Monitor Spool Action: Verify spools return to the appropriate positions during operation.
Build Better Systems with Reliable Directional Control Valves
Choosing the right directional control valve can streamline your operations, reduce downtime, and improve overall system performance. Whether you're tackling a single-acting task or managing complex double-acting machinery, understanding these components ensures you get the most out of your hydraulic system.
Are you ready to take performance to the next level? Explore Bailey International’s diverse range of hydraulic solutions, including premium directional control valves designed to keep you moving forward seamlessly. With expert support and custom engineering options, Bailey International is your trusted partner in hydraulic innovation.
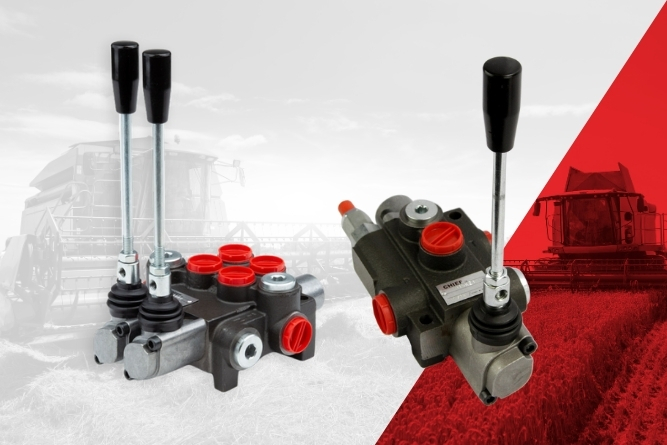
Everything You Need to Know About Directional Control Valves
Hydraulic cylinders are the backbone of heavy equipment operations, found everywhere from construction machinery to agricultural tools. While they may seem like simple components, their production process combines precision, engineering excellence, and stringent quality standards.
Step 1: Receiving and Inspecting Raw Materials
The process begins with raw materials, primarily steel, which arrive in bulk at the manufacturing facility. At Bailey’s Knoxville facility, for instance, over 40,000 lbs of raw steel are received weekly. However, not all that glitters is gold, and not all steel is fit for use.
Quality Assurance
Every incoming batch undergoes rigorous inspection in the Quality Assurance (QA) Lab. This involves verifying material certifications and running tests to ensure the steel meets required specifications. Advanced tools like Faro Arm and 3D scanners create ultra-precise digital blueprints, ensuring every material aligns with optimal tolerances.
Why it matters: Even a small defect in raw material could weaken a cylinder’s performance under high-pressure environments, possibly leading to catastrophic failure.
Step 2: Machining – Precision Above All Else
After the QA checks, the raw material moves to the CNC machining stations. Here, the material undergoes lathing, milling, and drilling to transform it into finely tuned components like tubes, rods, and end caps.
What happens during machining?
- Boring and Threading: CNC lathes create internal bores and threads with pinpoint accuracy. This ensures cylinders achieve perfect seals when assembled.
- Drilling: Holes are drilled into the rods and cylinder tubes at specific angles to integrate ports and attachments.
- Deburring: Edges are smoothed, ensuring no sharp fragments remain, which could damage seals later.
At Bailey, advanced CNC machines can produce up to 120 smaller tubes per day or run larger 8-inch tubes within approximately 8 minutes per piece, drastically cutting production time.
Step 3: Welding – Fusing Strength
Following machining, individual components move to the welding stations, where they are expertly assembled into a cylinder body. MIG and TIG welding, along with robotic welders, ensure strong, durable joints that can withstand extreme pressures.
The accompanying QA process involves verifying that each weld adheres to precise dimensions and structural integrity standards. During inspections, unacceptable seams are flagged immediately and rectified.
Why it matters: Flawless welding is critical for maintaining structural integrity, especially in applications that routinely involve forces of several thousand PSI.
Step 4: Assembly – Bringing it All Together
Once the individual components are complete, the hydraulic cylinder is ready for assembly. Skilled technicians fit seals, rods, and other elements into the cylinder body while ensuring all parts remain contamination-free.
Assembly Highlights
- Seal Installation: High-quality rubber seals are placed with precision to prevent leaks.
- Lubrication: Components are lubricated as required, ensuring smooth operation over extended durations.
- Torque Testing: Bolts, threads, and ports are tightened to exact specifications, ensuring every element fits perfectly.
Assembly teams often work hand-in-hand with QA staff for real-time inspections and corrections at every station.
Step 5: Rigorous Testing – One Cylinder Fit for All
One of the most critical stages in the production process is testing. At Bailey, every cylinder undergoes pressure testing at 1.5 times operating capacity—up to 7500 PSI—to ensure durability and reliability under extreme conditions.
Types of Tests
- Pressure Testing simulates real-world conditions.
- Leak Testing ensures seals maintain integrity under stress.
- Performance Checks verify smooth motion across the cylinder's operational range.
Only after passing these rigorous tests can a cylinder move on to coating and finishing.
Step 6: Coating and Customization
Now that the manufactured cylinder has been tested, it’s prepared for environmental longevity and visual appeal through the painting process. At Bailey, customers can even request custom colors.
Why Paint Matters
The paint layer protects the cylinder against rust, corrosion, and environmental wear, extending its lifespan significantly.
Step 7: Packaging and Shipping
Finally, the finished hydraulic cylinders are meticulously packaged and prepared for shipment. Whether destined for an OEM, distributor, or field mechanic, each cylinder includes clear labeling and accompanying documents like specs and test reports. With Bailey’s strategic warehouse locations and streamlined logistics, components reach most customers within just two days.
Why Precision Matters in Hydraulic Cylinder Manufacturing
The process of creating a hydraulic cylinder is more than just an assembly line; it’s a calculated, carefully monitored sequence of operations. Every step, from selecting raw materials to delivering the finished product, determines the hydraulic cylinder’s overall lifespan, efficiency, and reliability in real-world applications.
Whether you're sourcing cylinders for manufacturing, agriculture, or heavy equipment, choose trusted providers like Bailey International, who prioritize precision, quality, and durability.
Discover Excellence with Bailey International
Want premium hydraulic cylinders that guarantee peak performance? Bailey International delivers unmatched reliability backed by over 40 years of expertise. Explore their extensive range of hydraulic solutions today.
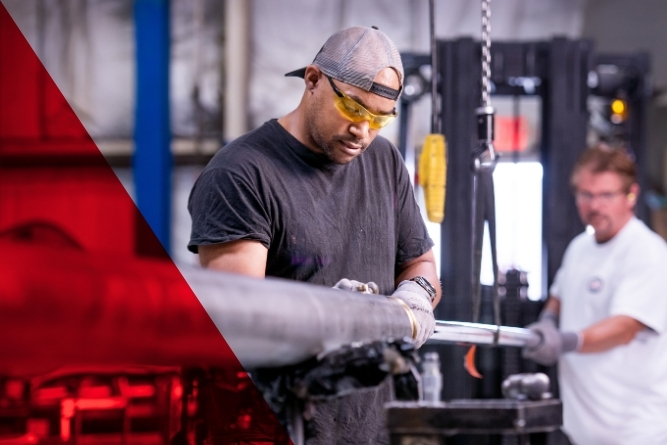
From Raw Materials to High Performance: How a Hydraulic Cylinder is Made
For engineers and technicians working with hydraulic systems, precise measurements are crucial to ensure optimal performance. Measuring a hydraulic cylinder correctly is an essential skill that helps you choose the right component for the job, guaranteeing safety, efficiency, and reliability. This guide outlines the key steps to measure a cylinder effectively, with insights from Bailey International, a trusted name in hydraulic solutions for over 40 years.
Why Accurate Measurement Matters
Hydraulic cylinders are used across industries like agriculture, construction, manufacturing, and transportation. An inaccurately measured cylinder can lead to inefficiencies, decreased performance, or even mechanical failures. Taking precise measurements ensures that the cylinder you choose will meet the demands of your specific application.
Key Measurements for Hydraulic Cylinders
1. Retracted Dimension
The retracted dimension is one of the most important metrics for selecting a hydraulic cylinder. This measurement determines the cylinder's length when fully closed.
How to Measure:
- Start by identifying the center of the pin at one end of the cylinder.
- Measure to the center of the pin at the other end, ensuring the cylinder is fully retracted.
Why It Matters:
The retracted dimension ensures that the cylinder fits within the designated space when not in use. This is particularly critical for applications with limited installation space, such as compact agricultural equipment or industrial machinery.
2. Stroke Length
The stroke is the distance the piston rod travels out of the cylinder. Think of the stroke as the functional movement of the cylinder.
How to Measure:
- Measure from the center of one work port to the center of the other work port.
- Deduct approximately two inches from your measurement to account for the piston inside the cylinder.
Why It Matters:
The stroke length determines how much linear motion the cylinder can deliver. Accurate stroke measurements are essential for applications where precision and range of motion are critical, such as material handling or ground support equipment.
3. Bore Dimension
The bore dimension refers to the inside diameter of the cylinder tube. This measurement is directly related to the push force the cylinder can generate.
How to Measure:
- Determine the inside diameter of the tube that encases the body of the cylinder.
Why It Matters:
The bore dimension defines the hydraulic cylinder's capacity to generate force. Larger bore sizes result in greater push forces, making this measurement vital for high-load applications like mining or construction industries.
Additional Considerations for Cylinder Selection
While retracted dimensions, stroke lengths, and bore dimensions are the primary measurements, here are a few additional factors to keep in mind:
1. Operating Pressure
Hydraulic systems operate under various pressure levels. Always ensure the cylinder you select can handle the operating pressure specified for your application. Bailey International offers detailed specifications for all of its products to help you make an informed choice.
2. Mounting Options
The type of mounting (e.g., clevis, flange, trunnion) affects how the cylinder interacts with the surrounding components. Make sure the mounting style aligns with your machinery's design.
3. Rod Material and Finish
The material and surface finish of the piston rod determine its resistance to wear and corrosion. Applications exposed to harsh environments, like marine or mining operations, may require specialized coatings or treatments.
Common Applications of Hydraulic Cylinders
Accurate measurements ensure that your cylinder performs reliably across a wide range of industries:
- Agriculture: Soil preparation, plowing, or hitch systems
- Construction: Heavy machinery like excavators and cranes
- Material Handling: Forklifts or conveyor systems
- Industrial Operations: Press machines and automated systems
- Transportation: Brake and suspension systems for railroads
Hydraulic systems can vary significantly depending on their applications. If you're unsure about measuring a hydraulic cylinder or selecting the right one, Bailey International's team of experts is here to help. With over four decades of experience and a vast catalog of hydraulic components, Bailey provides solutions you can trust.
Why Choose Bailey International?
Bailey isn't just a supplier—it's a partner for success. Here’s how Bailey stands out:
- Unmatched Expertise: Over 40 years of experience in hydraulic and electronic solutions.
- Custom Solutions: If standard components don’t match your needs, Bailey's MVP Program offers fully customized options.
- Reliable Support: From design to delivery, Bailey provides comprehensive assistance to ensure optimal performance.
- Fast Shipping: Strategically located warehouses allow Bailey to deliver components quickly, minimizing downtime.
Browse Bailey's hydraulic cylinders and more at www.baileyintl.com.
Proper measurement of hydraulic cylinders is the foundation of any efficient and functional hydraulic system. By following the steps outlined in this guide, you can ensure that every measurement is precise and your cylinder selection is ideal for the task at hand.
When precision matters most, partner with a name you can rely on. Contact Bailey International for expert guidance or browse their extensive collection of hydraulic components to find the perfect fit for your needs.
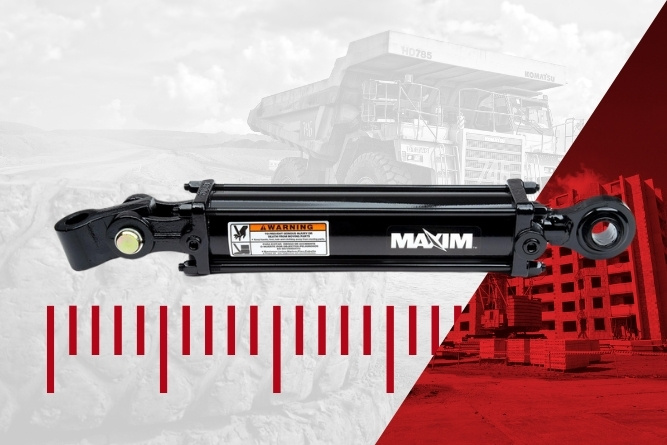
How to Measure a Hydraulic Cylinder
Understanding the precise specifications of a gear pump is critical for hydraulic engineers, technicians, and mechanics. Whether you need to replace an existing component, verify capacity, or plan for optimal system performance, knowing how to accurately measure your gear pump is an essential skill.
This guide provides step-by-step instructions on how to measure the cubic-inch displacement of a gear pump, using clear and accurate techniques that will save you time and ensure precision. Follow along for professional advice grounded in expertise and reliability.
What You'll Need
Before starting, ensure you have the following tools on hand:
- A caliper (digital or vernier for precise measurements)
- A clean work surface for disassembling the pump
- The gear pump in question
It’s also ideal to have a pen and paper or a device for recording your measurements and calculations.
Step 1: Disassemble the Gear Pump
To measure the cubic-inch displacement of a gear pump, you first need to access internal components. Follow these steps to carefully disassemble the pump:
- Remove the four bolts holding the pump together. Be sure to place the bolts in a secure location to avoid losing hardware during reassembly.
- Take off the end plate. This will expose the gear chamber.
- Proceed to remove the gear chamber, followed by the bearing carrier.
- Extract the gear itself carefully to avoid any potential damage. Handle these components with precision to maintain the structural integrity of each part.
- Finally, detach the front plate, allowing full access to the internal structure.
Properly disassembling the pump is critical to gaining accurate measurements. Ensure all components are clean and free of debris before proceeding to the measurement process.
Step 2: Take Precise Measurements
Now that the pump is disassembled, it’s time to collect the necessary dimensions to calculate the cubic-inch displacement. Use your caliper for maximum accuracy and measure the following:
1. Length Across the Gear Chamber
With the caliper, measure the length of the gear chamber from top to bottom. Ensure the caliper is correctly aligned for a precise reading.
2. Diameter Across One Gear Chamber
Next, measure the diameter across one gear chamber. This dimension is crucial for calculating the circular cross-section, so accuracy is paramount.
3. Width of the Gear Teeth
Finally, measure the width of one gear itself. This measurement will factor into determining the overall volume the gear displaces as it rotates.
Keep your measurements recorded in consistent units—typically in inches for hydraulic applications in the U.S.—to ensure uniformity during the calculation process.
Step 3: Calculate the Cubic-Inch Displacement
Once you have each of these measurements recorded, you can determine the cubic-inch displacement using a simple formula. For a gear pump, the displacement generally follows this calculation:
Cubic Inch Displacement = π × (Chamber Diameter ÷ 2)² × Chamber Length × Gear Width
Here’s a breakdown of the formula:
- π (Pi): Constant (3.14159)
- Chamber Diameter ÷ 2: Determines the radius
- Chamber Length: The length of the gear chamber
- Gear Width: Thickness of the gear which defines the displacement during rotations
Calculate the result to determine the exact cubic-inch displacement of your gear pump. This number provides crucial insight into the pump’s capacity and helps match it to the right hydraulic system requirements.
Why Accurate Measurements Matter
Correct measurements of a gear pump are key to achieving optimized hydraulic system performance. Here’s why it’s important:
- System Efficiency: Understanding displacement ensures your pump meets the flow rate requirements of your system.
- Preventing Overloading: A mismatch in capacity could lead to pressure imbalances, causing undue stress on other components.
- Improved Component Longevity: Proper sizing and matching minimize wear and tear, extending system uptime and reducing costs.
By following these steps, you'll have the accurate data needed to maintain or enhance the efficiency of your hydraulic system.
Expert Support and Custom Solutions from Bailey
If you still have questions or require specialized assistance, Bailey International provides expert support backed by over 40 years of leadership in hydraulics. Our seasoned team is dedicated to helping you make informed decisions with tailored solutions for your unique needs.
Looking for a new gear pump to meet precise specifications? Browse Bailey’s extensive catalog of high-quality gear pumps, hydraulic valves, and other components designed to optimize your operations.
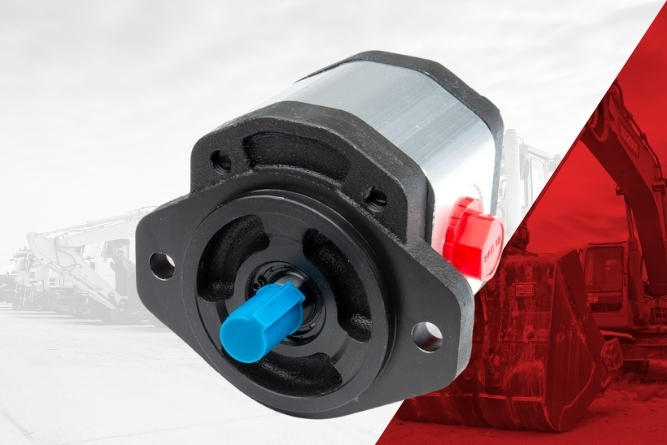
How to Measure a Gear Pump
Directional control valves are essential components in hydraulic systems, and understanding how to install one can streamline operations across various applications. Whether you're an experienced hydraulic engineer or a professional working in construction, ensuring the proper installation of a control valve is a fundamental skill. This guide will break down the process, highlight key considerations, and provide insights into efficient hydraulic valve installation.
Why Directional Control Valves Matter
Directional control valves manage hydraulic fluid flow, allowing operators to control the direction and pressure within hydraulic systems. These are integral for applications like controlling actuators, motors, or cylinders in machinery. Proper installation ensures equipment reliability, system efficiency, and long-term performance.
Step-by-Step Guide to Plumbing a Directional Control Valve
Follow these steps to ensure the correct installation of your directional control valve.
Step 1. Identify Valve Components
Start by inspecting your valve. Look for clear labels for the pump line (P), tank line (T), and work ports. These designations guide the direction of hydraulic fluid flow and are crucial for effective setup.
- The pump line (P) connects to your hydraulic pump.
- The tank line (T) directs fluid back to the reservoir or tank.
- Work ports control the associated actuators or machinery.
Additionally, some valves include arrows indicating flow direction. Use these markings to double-check each connection point.
Step 2. Gather the Proper Tools and Materials
To streamline the installation, ensure you have the following tools and materials ready:
- Hydraulic hoses and fittings.
- Wrenches suitable for your valve's connections.
- Thread sealant or PTFE tape to prevent leaks.
- A clean workspace to avoid dirt or contaminants entering the system.
Step 3. Connect the Pump Line to the Valve
Locate the P (pump line) port on the valve and securely attach the hydraulic line connected to the pump. This line supplies pressurized fluid to the system, so double-check that the fittings are tight and free from leaks to avoid pressure loss.
Step 4. Attach the Tank Line
Next, connect the T (tank line) port on the valve to the hydraulic tank or reservoir. This line provides a return path for the fluid after completing each cycle. Proper connection avoids fluid buildup and ensures system efficiency.
Step 5. Connect Work Ports to Machinery
On top of the valve, you’ll find the work ports, which control actuators, such as a hydraulic cylinder, motor, or other components. Each work port directs hydraulic fluid to corresponding equipment. Double-check the connections to match your system's specifications and verify that the direction of flow aligns correctly for desired operations.
Step 6. Secure and Test the System
Once all connections are complete, secure the valve in place, ensuring it is firmly mounted to prevent movement. Turn on the hydraulic system and perform a preliminary test:
- Check for leaks around the connections.
- Verify that fluid flows in the correct direction.
- Operate actuators to ensure proper control and functionality.
Testing ensures that your setup is accurate and prevents future operational issues.
Common Mistakes to Avoid
When plumbing a directional control valve, there are a few common pitfalls to watch out for:
- Reversed Connections – Attaching the pump line to the tank port or vice versa will result in system failure. Always double-check labels and flow directions before proceeding.
- Loose Fittings – Improperly tightened connections can cause leaks, inefficiency, or even complete system shutdown.
- Neglecting System Pressure Ratings – Ensure the valve you’re using matches the pressure and flow requirements of your hydraulic components.
Optimizing Valve Installation with Expert Support
If you’re a professional looking to simplify hydraulic installations or require tailored solutions, consider working with industry experts like Bailey International. With over 40 years of experience, Bailey provides high-quality hydraulic components, reliable technical support, and custom solutions for diverse industries, including construction, agriculture, and transportation.
Visit Bailey International to explore their product catalog and elevate your hydraulic systems today.
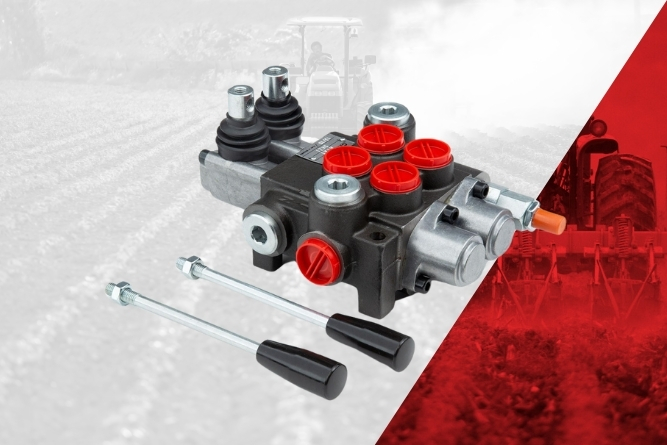
How to Plumb a Directional Control Valve
Properly calibrating your hydraulic system is essential for maintaining efficiency, safety, and performance. One critical aspect is setting your relief pressure. This process ensures your system is working correctly and prevents damage caused by over-pressurization.
If you’re new to hydraulic system maintenance or just need a refresher, this guide will walk you through how to set your hydraulic system's relief pressure step-by-step. We’ll make sure you understand what’s required and empower you to get it right every time.
Why It’s Important to Set the Relief Pressure Properly
Relief pressure acts as your system’s safety net. When hydraulic fluid pressure rises too high, it can damage hoses, pumps, cylinders, and other components. High pressure may also increase wear and tear, reduce the lifespan of your hydraulic system, and compromise safety.
By setting your relief pressure correctly, you ensure that your equipment runs efficiently without unnecessary strain on its components. Additionally, having the right pressure protects operators and the surrounding environment from the risks of a pressure-related failure.
Follow these carefully outlined steps, and you’ll have your system calibrated safely and effectively.
Step 1: Determine Your System’s Current Pressure
Start by finding out your hydraulic system’s existing pressure level. To do this, you’ll need to operate the system and use a pressure gauge to monitor the pressure. Create pressure in the system by activating it as you would during normal operations, watching the pressure gauge for measurements.
Important Tips:
- Always use a high-quality and calibrated pressure gauge for accurate readings.
- Ensure the gauge is compatible with your specific hydraulic system to avoid errors.
Knowing your current pressure is vital for adjusting the relief pressure to meet your specific equipment's requirements.
Step 2: Consult Your Equipment Manual for Pressure Requirements
Not all systems operate at the same pressure. The correct relief pressure will depend on the type of equipment you’re working with and its specific application. Check your equipment’s product manual or contact the manufacturer for guidance on recommended pressure levels.
Pro Tip: When in doubt, don’t guess. Start low and gradually increase pressure if you lack clarity on the requirements, as over-pressurization could damage your system.
Step 3: Relieve Pressure and Loosen the Jam Nut
Before making any adjustments, power down the system or ensure that it is not under any pressure. Once the system is off, locate the directional control valve, specifically the relief valve assembly, within the hydraulics mechanism.
Now, loosen the jam nut (sometimes called a locknut) by turning it counterclockwise. This allows you to adjust the relief valve safely and effectively.
Safety Reminder:
- Wear PPE (Personal Protective Equipment) while working on hydraulic systems.
- Confirm that all moving components have stopped before loosening any parts.
Step 4: Adjust the Relief Valve Screw
Using a screwdriver or the appropriate tool for your valve, adjust the relief valve screw to increase or decrease the pressure. Here’s how it works:
- Turning clockwise increases relief pressure.
- Turning counterclockwise decreases relief pressure.
Tip: Small changes can have a dramatic effect on your system. Begin with slight turns to see how the pressure changes. For most valves, a quarter turn is sufficient to make significant adjustments.
Step 5: Tighten the Jam Nut and Test the System
Once the adjustment screw is in the correct position, tighten the jam nut to secure it. Without turning the screw further, carefully start your system back up. Gradually apply pressure while monitoring the system’s pressure gauge closely.
- If the system pressure meets your requirements, you’re done!
- If it’s too high or low, don’t worry. Repeat the adjustment process by loosening the jam nut and fine-tuning the screw until the desired relief pressure is achieved.
Step 6: Test and Verify
It’s essential to double-check your work for accuracy and safety. Operate your hydraulic system under normal working conditions and keep an eye on the pressure gauge for any unexpected fluctuations. Once everything is stable and functioning within your equipment’s recommended pressure range, the setup is complete.
Troubleshooting:
- Does the pressure still exceed the target range? Reinspect the relief valve to ensure everything is properly secured and adjusted.
- Is the gauge reading staying too low? There may be other components contributing to insufficient pressure, such as blockages or a malfunctioning pump.
Tips for Success
- Document your changes. Keep a record of the final relief pressure you set. This will make future calibrations easier to perform.
- Schedule regular checks. Relief valves can wear out over time if your system is exposed to demanding operations. Routine checkups ensure they remain effective.
- When in doubt, call the experts. The hydraulic specialists at Bailey International are ready to guide you through troubleshooting and provide tailored recommendations for your system.
Achieving Precision with Bailey International
Setting your hydraulic system relief pressure is a fundamental step in maintaining safety, efficiency, and longevity. But it doesn’t end there. At Bailey International, we deliver solutions tailored to your specific needs—whether it’s sourcing top-tier components or providing expert advice.
From directional control valves to pressure gauges, our extensive product range has the tools and resources you need to ensure smooth operations.
Looking for more guidance? Explore our educational resources or talk to one of our technicians today to ensure your systems operate at peak performance.
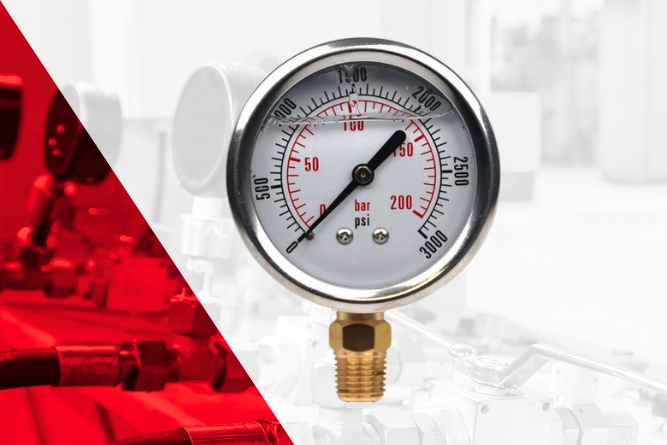
How to Set Your Hydraulic System Relief Pressure
When it comes to hydraulic systems, gear pumps are the heart of countless applications across industries, like construction, oil & gas, and manufacturing. With their durability, efficiency, and reliability, gear pumps are among the most widely used pumps in the world today. This guide explains what sets gear pumps apart, how they work, and how to get the best performance from them in your hydraulic systems.
What Are Gear Pumps?
A gear pump is a type of positive displacement pump that uses the meshing of gears to pump oil or other fluids. Their primary function is to generate flow, while the resistance—caused by valves, motors, or cylinders in the system—creates the necessary pressure to drive the operation.
Key characteristics of gear pumps:
- Durability: Gear pumps can handle contaminated fluids better than many other pump types, making them ideal for demanding environments.
- Affordability: They are generally more cost-effective than vane or piston pumps, making them a popular choice for many applications.
- Simplicity and Reliability: With fewer complex components, gear pumps are easier to maintain and highly reliable under continuous use.
How Do Gear Pumps Work?
The operation of gear pumps follows a straightforward and highly efficient process:
- Intake of Fluid: The gears rotate, creating a vacuum that draws oil into the pump.
- Movement of Fluid: The fluid is carried around the outer chamber of the pump, trapped between the gear teeth and housing.
- Pressurization and Output: The gears' rotation pushes the fluid out through the outlet port, creating flow within the hydraulic system.
Gear pumps have a fixed displacement, which means the same amount of fluid is moved per rotation of the gears. This displacement is measured in cubic inches or cubic centimeters, depending on the application.
Watch a gear pump in action by checking out our demo video on one of our gear pump solutions.
Types of Gear Pumps
Gear pumps come in a variety of shaft designs to meet the needs of specific applications. Common types include:
- Spline Shaft Pumps: Features multiple teeth for efficient torque transfer.
- Keyed Shaft (KY) Pumps: Uses a key to lock the shaft and gear together for secure operation.
- Tang Shaft Pumps: Ideal for specific, precise applications requiring unique shaft configurations.
Regardless of the shaft type, the functional principles of gear pumps remain the same.
Applications of Gear Pumps Across Industries
1. Construction
From excavators to bulldozers, gear pumps are the driving force behind the hydraulic systems that power heavy construction equipment. Their durability and ability to handle contamination make them ideal for rugged construction environments.
2. Oil & Gas
Gear pumps play a crucial role in upstream and midstream oil and gas operations, handling tasks such as fluid transfer and pressure boosting. Their reliability ensures uninterrupted operations in mission-critical environments.
3. Hydraulic Engineering
For hydraulic engineers designing cutting-edge systems, gear pumps offer a balance of simplicity and performance. They provide reliable flow generation, forming the foundation of any efficient hydraulic setup.
Installation Tips for Gear Pumps
Proper installation is critical to ensure long-term performance and reliability. Follow these steps for optimal setup:
- Align the Shaft: The pump shaft must be concentric with the driving motor or engine to avoid misalignment and wear.
- Select the Right Coupler: Use an appropriate coupler to securely connect the pump to the motor. Bailey offers a range of foot mounts, brackets, and couplers tailored to your needs.
- Use Clean Oil: Contaminants can wear down the gears over time. Employ a suction strainer and a filter to keep the hydraulic fluid clean.
- Secure Mounting: Proper mounting ensures stability and prevents unnecessary vibrations or stress on the pump.
Need assistance choosing the right components? Contact Bailey’s technical team for free expert guidance.
Maintenance Best Practices for Gear Pumps
Even the most durable pumps require regular maintenance to maximize their lifespan and efficiency. Here are a few best practices:
- Keep the Fluid Clean: Regularly replace or clean filters and strainers to prevent contamination.
- Inspect Seals: Leaky seals around the shaft or housing can lead to inefficiency. Replace worn-out seals promptly.
- Monitor for Wear: Check gears and other internal components for signs of wear and replace them as needed to avoid a complete pump failure.
- Service Schedule: Establish a routine maintenance schedule to proactively address issues before they become critical.
Gear pumps from Bailey are designed to last for years with proper care. Our experts can help extend your pump’s life by providing replacement parts, such as seals and couplers.
Bailey’s Gear Pump Solutions at a Glance:
- Premium Quality: High-performance materials and precise engineering.
- Custom Solutions: Tailored components to meet your unique requirements.
- Expert Support: Dedicated technical assistance for seamless installation and maintenance.
Boost efficiency and reliability in your hydraulic systems by choosing gear pumps from Bailey. Contact us or explore our online catalog to find the perfect solution for your application.
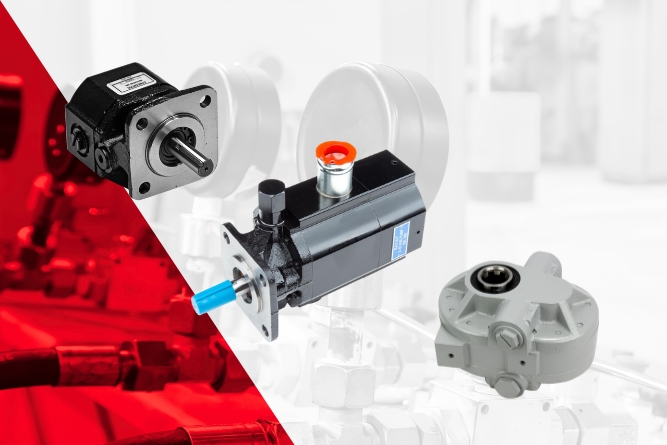
The Essential Guide to Gear Pumps for Hydraulic Industry Professionals
Hydraulic applications are integral to industries such as construction, agriculture, mining, and manufacturing. The systems powering these machines rely on precise controls to perform efficiently and reliably. Yet, as these industries evolve, off-the-shelf hydraulic controls often fall short of meeting the unique challenges and demands of specialized machinery. That’s where custom hydraulic controls step in, offering tailored solutions to enhance performance, safety, and efficiency.
Here, we’ll explore the importance of customized hydraulic controls, highlight their key benefits, and introduce you to Bailey Electronics, a leader in tailored solutions for electronic hydraulic applications.
Why Customization Matters
Off-the-shelf hydraulic controls might seem like a convenient choice. However, most standard options are designed with broad applications in mind, leaving gaps in performance for specialized needs. Here’s why customization is essential for hydraulic applications:
- Unique Machine Requirements
Every hydraulic machine has specific performance requirements. Off-the-shelf controls may not provide the precision and responsiveness needed to meet those demands.
- Operational Efficiency
Standard controls can lead to inefficiencies as they lack the adaptability to meet real-world operating conditions.
- Industry-Specific Demands
Equipment used in construction, mining, and agriculture faces unique challenges such as harsh environments and high operating pressures. Custom controls are built to withstand these conditions, ensuring durability.
Custom hydraulic controls address these gaps, providing a tailored fit for the operational needs of complex machinery.
Benefits of Custom Hydraulic Controls
Tailored hydraulic controls deliver several advantages over generic alternatives, boosting overall machine performance:
1. Enhanced Performance
Custom controls are designed for precision, delivering smoother motion, quicker response times, and greater overall system accuracy. This is critical for applications like material handling, where small errors can disrupt workflows.
2. Improved Safety
With custom designs, safety features can be integrated to match specific operational risks. For example, emergency stop systems or controls with better ergonomics reduce the likelihood of accidents, keeping operators safe.
3. Maximum Efficiency
Tailored solutions reduce energy consumption by ensuring that hydraulic systems only operate within their optimal parameters. This lowers costs while extending equipment lifespan.
4. Operator Comfort
Human-centric designs, such as ergonomic joysticks and armrests, prioritize operator comfort and reduce fatigue, enabling longer and more productive working hours.
5. Scalability and Adaptability
Custom controls allow for integration with modern technologies, such as IoT (Internet of Things) sensors, to offer real-time data tracking, enabling proactive maintenance and flexible system upgrades.
These advantages aren’t just desirable—they’ve become necessary for businesses looking to stay competitive in demanding markets.
Meet Bailey Electronics
When it comes to custom solutions, Bailey Electronics sets the gold standard. With decades of experience and a global reach, Bailey works closely with machinery manufacturers, industrial designers, and engineers to deliver tailor-made hydraulic controls that exceed expectations.
Expert Engineering
Bailey Electronics boasts a team of highly skilled engineers who specialize in creating innovative solutions for diverse hydraulic applications. Their deep industry knowledge allows for precise customization based on each client’s specifications.
Global Reach, Local Expertise
Serving industries worldwide, Bailey Electronics combines its global expertise with a commitment to local customer needs. Whether you’re designing agricultural machinery or manufacturing equipment for mining operations, Bailey supports you with tailored solutions and unmatched reliability.
Quality and Rigorous Testing
Bailey Electronics places an unwavering emphasis on quality. Every product is built with premium materials, including high-grade metals, plastics, and electronic components, designed for unmatched resilience in their field.
Stringent Quality Standards
Bailey Electronics subjects all products to rigorous testing protocols to ensure compliance with the highest industry standards. These tests cover durability, performance, and safety, so customers can trust their products in even the most challenging conditions.
Certified Excellence
Bailey Electronics is proud to hold ISO certifications, including ISO 9001 for quality management, ISO 14001 for environmental management, and ISO 45001 for occupational health and safety. These certifications reflect the company’s steadfast dedication to delivering superior, reliable solutions.
When you choose Bailey Electronics, you’re not just investing in a product—you’re investing in peace of mind.
Customization That Meets Your Needs
At Bailey Electronics, customization is not an afterthought—it’s their core strength. Their client-centric approach ensures that every solution is tailored precisely to meet specific challenges.
- End-to-End Collaboration
Bailey Electronics works closely with clients every step of the way, from ideation to delivery. Their engineers ensure the final product aligns perfectly with your operational goals.
- Wide Range of Customizable Products
Whether you need joystick controls, throttle systems, or hydraulic sensors, Bailey Electronics offers a diverse range of customizable components to fit seamlessly into your machinery.
- Future-Forward Solutions
Bailey’s custom controls are designed to integrate with advanced technologies, ensuring compatibility with IoT systems, automation, and other modern engineering advancements.
Your needs are never generic—why should your hydraulic controls be?
Make the Switch to Custom Hydraulic Controls
Hydraulic systems drive productivity, safety, and efficiency across industries. Custom controls take this a step further, allowing businesses to optimize performance, meet specific operational challenges, and ensure long-term reliability.
Bailey is your trusted partner in creating custom hydraulic controls tailored to your unique requirements. With their dedication to engineering excellence, quality standards, and client collaboration, they’ve earned their place as a leader in the industry.
Don’t settle for less. Experience the difference custom controls can make for your hydraulic applications. Contact Bailey Electronics today to explore tailored solutions designed to power your success.
[Call to Action Button] Learn More About Custom Controls
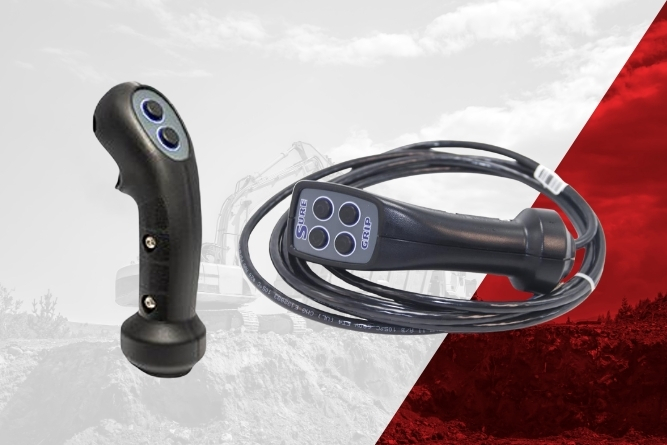
The Importance of Custom Controls for Your Hydraulic Applications
Hydraulic motors play a pivotal role in modern hydraulic systems, delivering the rotary force required to power machinery across industries. Whether you're an engineer designing industrial equipment, a hydraulic technician troubleshooting systems, or a construction professional seeking reliable components, understanding how hydraulic motors work and their applications is essential. This guide offers an in-depth look at hydraulic motors, from their mechanics to their practical uses, and tips for ensuring you're using the right motor for the job.
What Are Hydraulic Motors?
Hydraulic motors are key components in hydraulic systems, transforming fluid energy into mechanical energy. Essentially, they take pressurized fluid, often oil, and generate torque and rotational force to drive machinery. These motors are classified as actuators, meaning they operate at the end of the hydraulic line to perform a specific task—in this case, producing rotary motion.
For example:
- A hydraulic cylinder converts fluid power into linear motion, ideal for tasks like lifting or pressing.
- A hydraulic motor, meanwhile, manipulates fluid energy for rotary motion, offering torque to spin wheels, conveyor belts, or other components.
Types of Hydraulic Motors
The BM series motors, like those at Bailey International, exemplify versatility and strength in hydraulic motor design. Specific motor variations include:
- G-Rotor Motors: Named for the internal rotor component, these offer effective torque through their innovative design.
- G-Roller Motors (with roller bearings): These enhance operational efficiency by offering smoother rotation and reducing internal friction.
Why Not Simply Use a Hydraulic Pump as a Motor?
While gear pumps can technically be used as motors, they are not designed to handle the stress and directional flexibility required of motors. Hydraulic motors are specifically built for tasks like running in series (e.g., multiple motors powering a conveyor belt) or operating under bi-directional conditions. Using a pump as a motor may create inefficiencies and increase wear over time, making it an unsuitable choice for complex tasks.
Key Applications of Hydraulic Motors
Hydraulic motors excel in various fields, providing essential power to drive systems in demanding situations. Here are some common applications across industries:
1. Construction Equipment
Hydraulic motors power heavy machinery such as excavators, cranes, bulldozers, and drills. Their ability to withstand high pressures and deliver consistent torque makes them ideal for operating under rugged conditions.
2. Conveyor Systems
Motors in the BM series, like those featured by Bailey, are perfect for conveyor applications. Picture a wood processing plant where multiple motors are placed in series to drive conveyor belts continuously, ensuring the smooth flow of materials.
3. Agriculture
Think of tractors or harvesters where hydraulic motors power rotating components like mowers or seed-drilling systems. These high-torque motors ensure reliable performance that's critical for large-scale farming operations.
4. Industrial Machines
From injection molding machines to presses, hydraulic motors are indispensable in ensuring industrial equipment operates with precision and efficiency.
5. Marine and Transportation
Hydraulic motors also play a significant role in ship steering mechanisms, winches, and vehicle applications where controlled rotary motion is essential.
Advantages of Using Hydraulic Motors
Why choose hydraulic motors for your applications? Here are some clear benefits:
- High Torque at Low Speed: Hydraulic motors can provide substantial force even at relatively low operational speeds.
- Durability: Designed to handle high pressures, these motors are built to last, even in challenging environments.
- Compact and Efficient Design: Hydraulic motors offer a high power-to-weight ratio, making them suitable for space-constrained setups.
- Bi-Directional Operation: Many motors, including Bailey’s BM series, can spin both clockwise and counterclockwise, offering versatility for different systems.
- Scalability: Motors come in various displacements and sizes, allowing engineers and technicians to find the perfect match for their specific needs.
Choosing the Right Hydraulic Motor
Selecting the right hydraulic motor for your application is crucial for ensuring operational efficiency and longevity. Here’s how you can make sure you’re getting the right fit:
1. Determine Your Performance Requirements
Understand your torque, speed, and pressure needs. This will help narrow down your motor choices by size and performance capacity.
2. Evaluate the Application
For example, if you need a motor for conveyor systems, consider whether the motor can be run in series and if it’s designed to handle pressure on both sides.
3. Account for Directionality
Choose motors that are bi-rotational if your system demands movement in both clockwise and counterclockwise directions.
4. Consider Motor Type
Decide between basic motors like G-Rotor and more advanced G-Roller motors, which offer greater efficiency and support for high-load applications.
5. Consult Experts
Reputable providers like Bailey International offer engineering support to help you determine the best fit. Their MVP (Motors, Valves, and Pumps) program simplifies the process for tailored hydraulic solutions.
Maintaining Hydraulic Motors for Longevity
Once you’ve selected the right motor, proper maintenance is vital to its performance. Here are a few tips:
- Regular Inspection: Check for leaks, worn components, or unusual noises during motor operation.
- Use Clean Hydraulic Fluid: Contaminated fluid can damage motor components over time.
- Follow the Manufacturer’s Guidelines: Adhering to prescribed operating conditions ensures optimal performance and prevents unnecessary wear.
Why Choose Bailey International for Hydraulic Motors?
Bailey International is a trusted leader in hydraulic solutions, with over 40 years of experience. Here’s why professionals turn to them for motors:
- Comprehensive Range: Bailey offers the BM series with various displacements and configurations to fit different needs.
- Expert Support: Their technical and engineering teams provide guidance on motor selection and troubleshooting.
- Reliable Warranty: All motors come with robust warranties, reflecting Bailey’s commitment to quality and performance.
- Quick Delivery: Strategically located warehouses ensure fast shipment, minimizing downtime.
If you’re unsure about which hydraulic motor is right for you, Bailey’s MVP center is just a call away, ready to assist with your project.
Optimize Your Systems with the Right Hydraulic Motor
Hydraulic motors are the backbone of countless industrial, agricultural, and construction systems. Whether powering conveyor belts or giant excavators, these components translate hydraulic energy into reliable rotary motion, enabling the seamless operation of complex machinery.
To ensure you get the right motor for your needs, focus on understanding your application, performance requirements, and system constraints. And if you need expert advice, Bailey International’s experienced team is here to help.
Find the perfect hydraulic motor for your application today. Contact Bailey or visit our website to explore our wide selection of hydraulic motors, including the BM series, and experience the Bailey advantage.
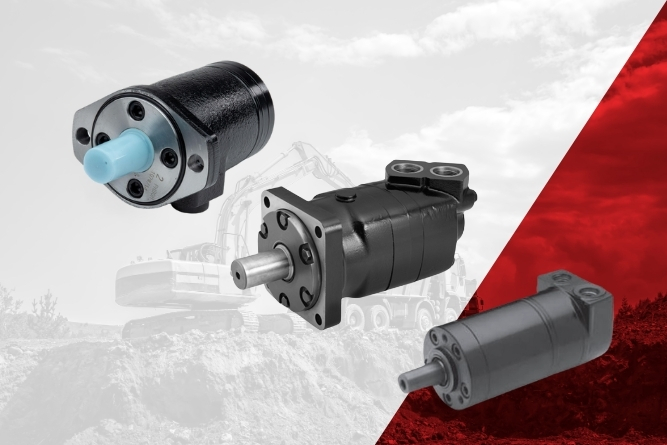
Understanding Hydraulic Motors and Their Applications
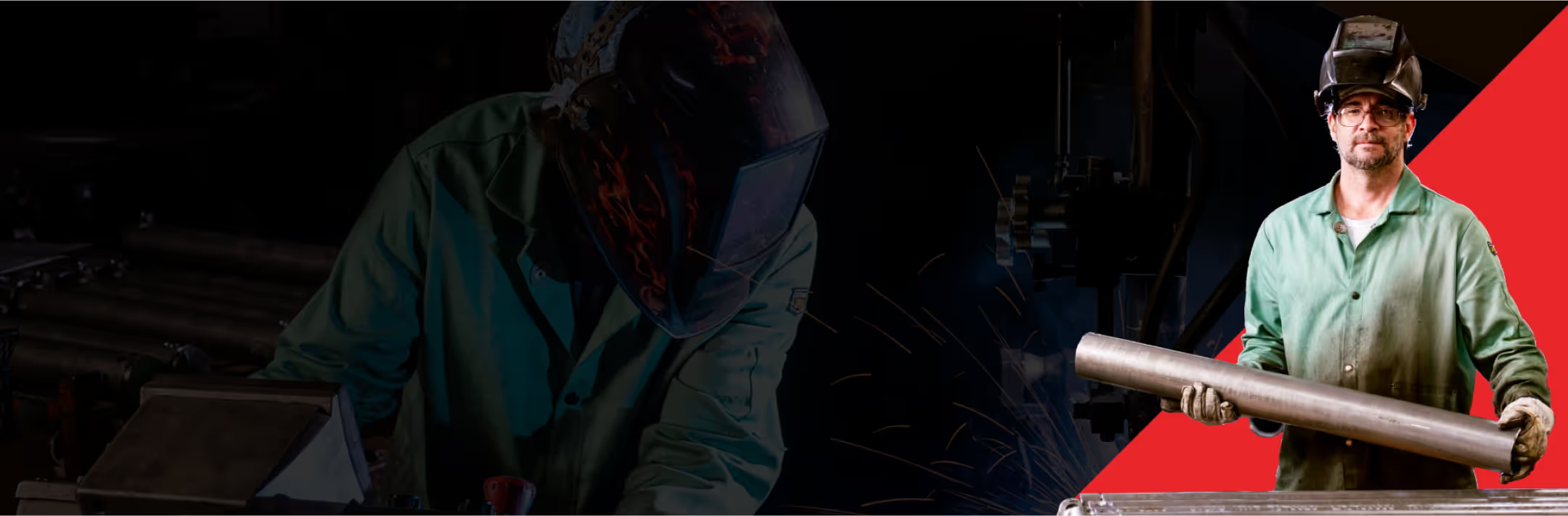
Customer Support, Engineer Expertise
Reliable support when you need it. Our team of customer service agents and engineers is dedicated to keeping your operations running smoothly. With expert guidance, technical resources, and Lunchbox training programs, we empower you to get the most out of your hydraulic products.
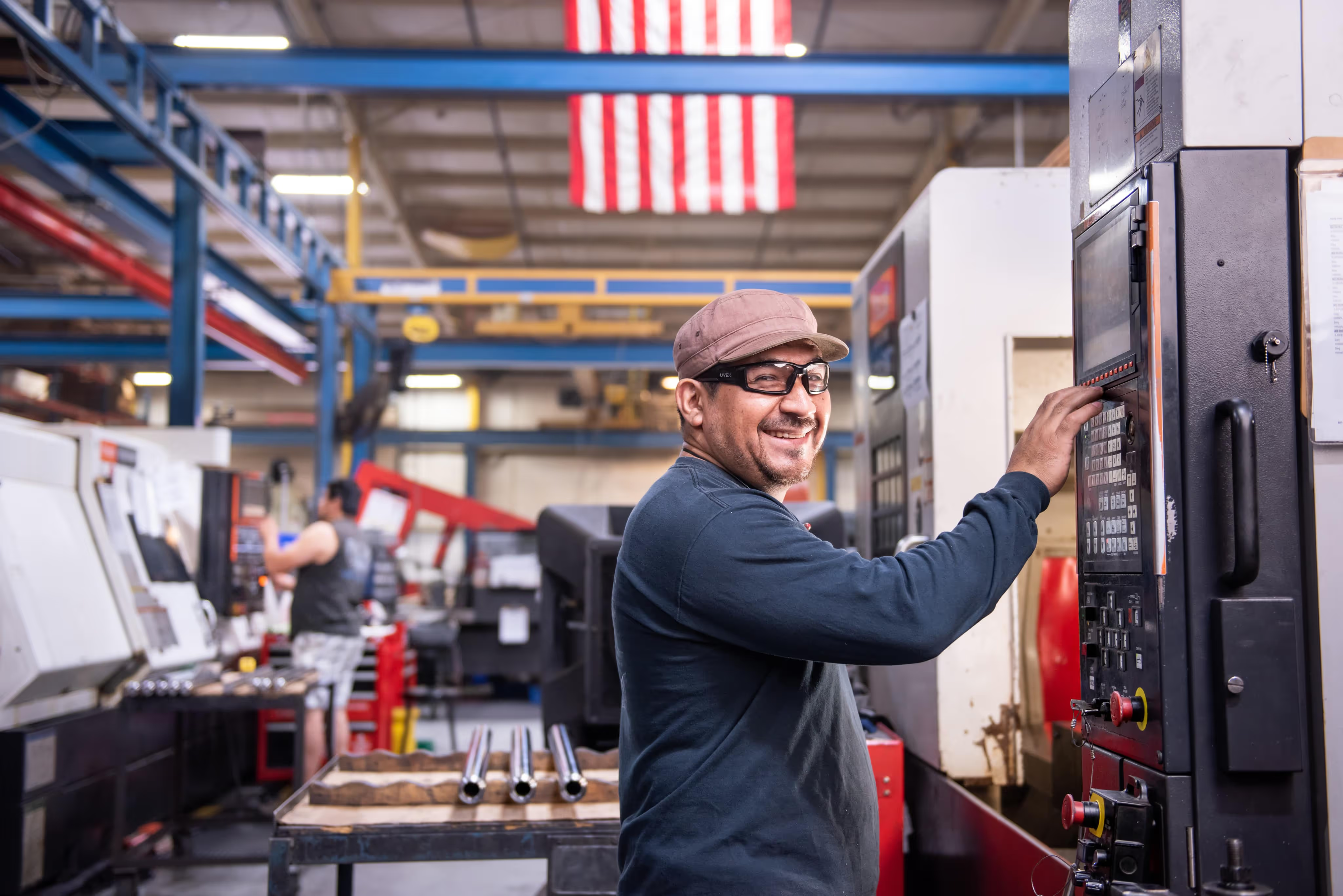